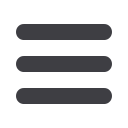

T
ube
B
ending,
H
ydroforming &
E
nd-
Fo
rming
124
M
ay
/J
une
2007
Unison, UK, has added a 100mm/4”
diameter, multi-stack CNC tube-bender
to its all-electric machine range. Called
Breeze-100, the machine is optimized for
high-precision applications, and includes
unique operating software. The company
claims that the machine virtually eliminates
the high costs normally associated with
machine configuration for precision small-
batch and just-in-time parts production.
Mr Alan Pickering, managing director of
Unison, says,
“This latest machine extends
the benefits of all-electric machines to new
applications including automotive and
aerospace manufacturing, and shipbuilding.”
Breeze-100 offers programmable control
over the rotary draw bending process
components, and thus can cold-bend
the most demanding materials with total
precision, such as 100mm/4" titanium
tubing. Bends of up to 180º can be made,
with a high degree of repeatability of
±0.05mm of distance between bends, and
±0.05º of bend angle, plane of bend or
rotation. This ensures good control of fluid
flow around tight bend radii and compatibility
with the hydroforming tools used in some
volume manufacturing processes.
A key element of the new machine is the
Unibend Control Software, which now
includes advanced features such as an
automatic setup routine. This automatically
senses and clamps a tube, ready for
bending – thus reducing initial setup time.
Users have complete
control over the bend
operation, and can
modify the standard
bend speed, clamping
pressure, pressure die
position and force, and
mandrel
positioning
parameters that are
applied to achieve the
ideal bend.
The machine includes
a webcam, which
Unison can remotely
access
over
the
internet. In combination
with a software ‘black
box’, which automatically stores the last 500
instructions entered by the operator, Unison
can help users to optimize their processes,
as well as provide remote maintenance.
Tube bending operations may be
programmed in three ways. They can be
automatically generated by transferring data
from CAD software, with interfaces for all
popular packages. A simple programming
template is also available, allowing users to
create a program by entering the distance
between bends, the angle of bend required,
and rotation of the tube. A further option
is copy or reverse engineering, by using
a tube measuring system to recreate the
coordinates from a sample or prototype.
The Breeze-100 uses servomotors to
control the bend process, including clamp,
pressure die, mandrel and follower. This
all-electric actuation provides significant
benefits related to energy consumption,
repeatability, and noise reduction. As the
actuation elements of the machine require
energy only when a bend is being made,
total consumption is greatly reduced.
In a measured comparison made by one
of Unison’s users, consumption showed a
ten-fold reduction. Further energy is saved
as Breeze machines can be switched off
when unused – avoiding the practice of
leaving hydraulic machines on when idle to
maintain oil temperature and consistency.
The new machine can be supplied to
interface with a manufacturer’s existing
tools, or as a turnkey system complete
with tooling. Unison also offers a range of
complementary equipment, allowing the
machine to be provided as a complete
automated cell, including downstream
equipment such as end-forming.
Unison
– UK
Fax
: +44 1723 582379
:
enquiries@unisonltd.comWebsite
:
www.unisonltd.comHorn Machine Tools
(US agent) – USA
Fax
: +1 559 431 4431
:
hmt@sierratel.comWebsite
:
www.hornmachinetools.comForming/rolling machine for corrugated tubes
The MPF rolling machine, from ORT Italia, is designed for corrugated tubes with
a stationary workpiece and rotating head. The machine has one rolling head with
three rotating corrugating tools, and is designed for a maximum corrugation length of
1,000mm and a tube diameter range from 6-20mm.
The MPF is designed for a fast and easy set-up and changeover, typically 10-15
minutes. Machine operation and part programming is undertaken via the machine PLC
with touch screen control panel.
Programming is user friendly and easy to learn, with minimal time required to create
complete programs for corrugating operations. Automatic loading and unloading
equipment is also available for tube lengths up to 1,000mm.
Established in 1964, ORT Italia is a leading manufacturer of tube rolling and forming
equipment, with over 4,000 installations worldwide.
ORT Italia SpA
– Italy
Fax
: +39 0374 370338
:
info@ortitalia.comWebsite
:
www.ortitalia.comLatest all-electric 100mm tube bender from Unison
fi
Unison’s Breeze-100, a new all-electric 100mm/4" tube bender
Breeze-100 can
cold-bend the most
demanding materials
with total precision,
such as 100mm/4"
titanium tubing
❱
❱