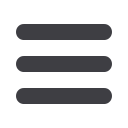

Technology
Update
42
M
ay
/J
une
2007
Shahid Bahonar Copper Industries Co,
Iran, has awarded a contract to Otto Junker
GmbH, Germany, for an indirect gas fired
roller hearth furnace for the bright annealing
of 15,000 tons per year of level wound coil
DHP copper tube. Shahid Bahonar Copper
Industries annually produces more than
45,000 tons of copper semi-manufactured
products, such as tubes, sheets and coils,
for use in second stage industries.
The contracted roller hearth furnace is
designed for the purpose of bright annealing
copper tube in the form of level wound coils.
It will be installed in the company’s new
copper tube production plant in Kerman,
Iran.
The level wound coils are individually loaded
onto trays which are then transported into a
stacking device which automatically stacks
the trays – up to a maximum of 5 trays per
stack. Following the stacking procedure, the
ends of the individual coils are connected
to the atmosphere distribution system of
the Otto Junker CTP system (copper tube
purging system).
The stack is then transported to the furnace
line via a cross conveyor. On the entry table
Hydropath Ltd, UK, manufactures a range
of water conditioning systems using
Hydropath technology. This technology
works by inducing coaxial electromagnetic
fields in the fluids passing through the
pipe.
A ‘wave’ is generated from the unit, which
is carried throughout the system, and this
charge helps prevent the electromechanical
process of corrosion taking place. The
negatively charged electrons
are drawn towards the outer skin
of the pipe (known as the ‘skin
effect’) whilst the heavier positively
charged ions are drawn away from
the service. The result is that a
state of passivity exists within the
water.
The
company’s
AquaKlear
system also provides the benefit
of killing bacteria and algae. It
does so by applying a charge to
the bacteria, which gets hydrated
with a pure water layer. This layer
is absorbed into the bacteria by osmosis,
creating osmotic pressure which bursts the
membrane thus killing the bacteria.
The Jordan Steel Factory outside Amman,
Jordan, was concerned about corrosion
within the pipework of its cooling system,
caused by large quantities of sulphate
reducing bacteria, iron oxides and scaling
build-up. These factors contributed to an
overall reduction in the efficiency of the
direct and indirect cooling system at the
factory.
The solution was to undertake an eight
month trial of Hydropath’s water conditioning
system. An AquaKlear P120 unit was fitted
to one of the pipes and a series of test
coupons installed throughout the system.
Seven carbon steel coupons with nuts and
bolts (made from the same material as the
pipes) were located throughout the system
to measure corrosion, and a further seven
stainless steel alloy coupons were affixed
with plastic nuts and bolts to measure scale
build-up. Plastic was used to eliminate any
interference from galvanic action.
Following the installation of the AquaKlear
P120 system, there was a significant
reduction in corrosion at the steel factory.
The results indicated a reduction of iron
oxide percentages in an eight month period
from 60-70 per cent to 49 per cent, which
reflected positively on reducing corrosion
rates. Scaling percentages also reduced
dramatically, leading to the more efficient
operation of the direct and indirect factory
cooling system.
Hydropath (UK) Ltd
– UK
Fax
: +44 115 986 9944
:
sales@hydropath.comWebsite
:
www.hydropath.comPreventing rust without chemicals
›
Hydropath’s AquaKlear P120 water conditioning system
Latest order for bright annealing
roller hearth furnace