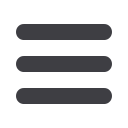

Technology
Update
53
M
ay
/J
une
2007
Switzerland, USA, Africa, Japan, Syria,
and Venezuela. Each country has its own
method of certifying weld procedure and
quality, and there are many additional
details to track when carrying out field
installations in other countries.
There are other complications, such as
in the food and beverage industry, where
some beverages can be quite caustic. The
repeatability and smoothness of the weld
on the interior of the tubes are the primary
reasons for using orbital welding. The end-
user must be convinced that no unevenness
exists that might cause corrosion to begin
and eventually rust through.
The training of Idroinox welders presents
another issue, concerning Italy’s labour
laws. In addition to a full workload at the
plant, the company has four teams
in the field: three in the food industry
and one in pharmaceutical. The
changing needs for experienced
programmers has resulted in a
creative solution: the company
has found that many experienced
welders do not want to adapt to
Idroinox’s mode of operation, so it
has turned to young people, often
with no welding experience, and
trains them according to its needs,
first in manual, then in automatic
welding.
In-house training results in three
types of welder. Group 1 is for
welders only qualified for manual welding.
Group 2 is for welders qualified for
automatic welding, but not for modifying
the combination of the various automatic
welding parameters. Group 3 is for welders
qualified to establish new programs and
procedures for the orbital welding systems.
All of the welders are expected to recognise
good and bad welds. The company has
7-8 welders who work primarily on manual
welding activities, but can operate orbital
welding systems, and are able to recognise
good welds, but make no changes to
the pre-established welding parameters.
Making an automatic weld with proven
qualified parameters is extremely easy.
Welding operators from Group 2 perform
automatic orbital welding, and are allowed
to change only those parameters considered
non-essential – ones that can be modified
without requiring the qualification of a
new welding procedure – allowing them to
compensate for variations in the work-piece
preparation. Visual checks are made, and a
sample is sent to be X-rayed. This procedure
ensures that the chosen and qualified
parameters stay within defined limits, in
order to avoid any kind of quality risks.
When welders have proven their ability,
Idroinox sponsors them for certification
with the Italian Institute of Welding under
ASME 9. Approximately 12 of Idroinox’s
20 welders are certified to establish new
weld procedures for the automated, orbital
welding systems.
The orbital welding machine is essential,
but the production procedures (eg how the
parts are prepared for the weld, and how the
machine is used) are even more important.
Cutting the tubes, cleaning them, the
methods and procedures used in the setup,
are all critical: automated orbital welding
is therefore a complete manufacturing
process.
Article supplied by Mr Dick Herzfeld, with input from
Mr Stefano Vitale, operations manager, Idroinox Impianti
Polysoude SAS
– France
Fax
: +33 240 681 188
:
info@polysoude.comWebsite
:
www.polysoude.comIdroinox Impianti Srl
– Italy
Fax
: +39 0521 604 010
:
sales@idroinox.itWebsite
:
www.idroinox.it›
Closed welding ‘K-Series’ head, adapted to
titanium applications in the aerospace industry
fi
The portable orbital power source used by
Idroinox
›
Smooth interior weld seam quality