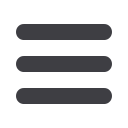

72
M
ay
/J
une
2007
T
ube
R
ussia –
28
-
31 M
ay
,
2007
›››
furnaces for annealing lines and continuous
annealing lines.
In the area of gas jet cooling technology
for steel tubes, the company has recently
modified a 15-year-old Ebner roller-hearth
furnace for boiler pipe production at
Zeleziarne Podbrezova in Slovakia.
This furnace is used for heat
treating
seamless-drawn
steel
tube at anneal temperatures of up
to 1,070°C, with a cooling rate of
300K/min in process atmosphere.
In addition to modernising the combustion
system in Zeleziarne’s furnace and
installing new hearth rollers, Ebner
installed a 2m-long quenching zone with
an atmosphere jet cooling and automation
system. The cooling gradient of 300K/min
can successfully achieve an austempered
bainite microstructure throughout the
6mm tube wall thickness without tube
deformation.
Ebner has also supplied the latest Hicon/
H2
®
roller-hearth automatic furnace for
Poongsan Corp in Korea, one of the world’s
largest producers of copper semi-finished
products.
An annealing facility for level-wound copper
tube coils has been installed at Poongsan’s
Ulsan works to meet increased quality
specifications. With a throughput of 3t/h,
the temperature scatter throughout the
charge is just +1.5°C by the end of the
soaking zone.
The gas-tight design of the furnace and
cooling section ensures low oxygen content
in the process atmosphere (2 per cent
hydrogen, balance nitrogen), and prevents
discoloration of coils. The cold/hot tube
purging system guarantees the lowest level
of contamination inside the tube, especially
on ‘inner grooved’ tubes.
A roller-hearth furnace, to process tubes in
straight lengths and in coil-form, has also
been installed at Buntmetall Amstetten.
Using the furnace, charge material is
annealed in process atmospheres at a
throughput of 2,000kg/h, with a maximum
furnace chamber temperature of 850°C.
The furnace can accommodate maximum
tube lengths of 11m, with operation in
semi-continuous or continuous mode. The
jet cooler section of the cooler was newly
developed specially for CuNi tubing.
Website
:
www.ebner.ccEFD Induction develops, commercialises
and supplies complete industrial heating
processes, including power sources,
mechanical handling equipment and control
systems based on the latest IT technology.
EFD Induction has emerged as a pioneer in
finding new induction heating applications
and solutions.
The Weldac G2 is the company’s family
of high-output solid-state welders. It is
available with output power of 150-2,000kW
and with 100, 200 and 300kHz nominal
frequencies. The Weldac uses rugged IGBT
transistors, which due to EFD’s patented
switching pattern, can now be used in
high-frequency applications, such as tube
welding. IGBT transistors are virtually
short-circuit proof, making the Weldac very
reliable and robust equipment that gives
more uptime and output.
Apart from capitalising on the strengths of
standardised IGBT transistors across the
entire frequency range, the Weldac G2
system also provides continuous electronic
load matching. Continuous electronic
load matching secures full power output
across a wide range of tube sizes, ensuring
maximum welding speeds for each size.
The Weldac eliminates the need for costly
compensation capacitors by using diode
rectifiers that result in a high, constant
power factor (0.95) at all power levels. Test-
verified efficiency from input at the rectifier
to output at the coil is 85-87 per cent.
Cooling water consumption is low, with no
need for expensive de-ionized water.
Website
:
www.efd-induction.comFounded in 1983, Elmaksan Ltd is one
of the leading Turkish companies in the
design and production of profile machines,
slitting machines and cut-to-length lines.
The company’s slitting lines can be used
on a range of materials including ferrous
metals, cold and hot carbon steel, stainless
steel, copper, brass, galvanised and other
types of metal alloys.
With the company’s pipe and profile lines,
the user can manufacture products with
different diameters. Easily changeable
equipment is used on these lines in order
to reach the fastest manufacturing speed. A
flying saw with high performance can also
be incorporated into pipe and profile lines,
according to user requirements.
Elmaksan’s
cut-to-length
lines
are
designed as manual or automatic, and are
intended to undertake sensitive packaging
using sheet and plastics. The company’s
machines are manufactured with the latest
versions of CAD (Auto-CAD), CAM (solid
CAM, master CAM, mechanical Cobra
design, Microstation) and other types of
design and construction programmes.
All departments, from engineering to
production, are linked to provide an
interactive manufacturing process and use
CNC lathing machines to reduce faults to a
minimum.
Website
:
www.elmaksan.netEMS, France, designs and builds special
tube end-forming and cutting machines,
which use techniques such as extrusion,
expanding, reduction, pushing, and
segment head/mandrel forming.
These machines are based on the highest
quality hydraulic and electrical components.
The company’s cutting machines are used
to recut bent tubes and to cut or recut
hydroformed tubes.
The company’s CT models cut without
material tearing or chips, using a
combination of two knives – one vertical
to pre-cut the tube, and one horizontal
Œ
EFD Induction AS
Norway
Stand FO-A03
›
The solid-state Weldac welder from EFD
Elmaksan Ltd
Turkey
Stand FO-E03
EMS
France
Stand B51
Œ