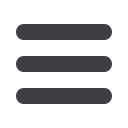

of the ASR series as well as a flow valve from the ASQ series. These
work in conjunction with a speed controller to assist with minimised
installation time, reduced mounting height and a more compact ma-
chine design. In using the company’s air saving valves, the following
benefits become apparent:
• Smooth operation of working and return strokes possible thanks
to speed consistency through the prevention of jerky movements
of working strokes
• Improved response time due to less delay of the return stroke by
the use of a quick supply and exhaust valve
• Easy piping as the body and one-touch fitting allows for 360 de-
gree rotations and the sealant on the male thread is standardised
• Pressure can be fixed (at 0,2 MPa) or variable (between 0,1 and
0,3 MPa)
Other applications for these air saving valves would be jerk preven-
tion in the vertical operation of a cylinder and quick air charge at the
end stroke for press applications.
Why so much air wastage?
According to a study conducted recently by the company based on
Europe’s consumption, the estimated annual industrial electricity
consumption is 400 TWh which is divided into three main energy
related categories:
E
nergy efficiency, in the past was… and for the foreseeable fu-
ture will remain … a hot topic. With end-users becoming more
and more discerning and government and economic policies
placing pressure on the business sector, the need for a competitive
advantage through lean manufacturing and new thinking becomes
crucial. Businesses are now under a proverbial microscope where
every output needs to be matched by a sustainable and efficient input.
SMC Pneumatics (further referred to as ‘the company’) has long
looked for innovative ways to reduce consumption. Amongst its array
of energy saving solutions and energy saving assessment tools and
software are air saving valves. These valves reduce air consumption
by up to 40% by operating the return stroke at a reduced pressure.
Conventional valve versus air-saving valve
According to Compressed Air Best Practices, as industrial automation
produces even more sophisticated technology with the advance of
robotics, benefits of weight reduction and power conservation, pneu-
matic valve designs have begun to find their role in a larger strategy
of environmental technology. The company invests 6% of its annual
turnover back into R&D each year. Today, alternatives exist and are
being designed and bettered on an ongoing basis. As valves evolve
to meet needs along with modifications to most pneumatic compo-
nents taking place on a very regular basis, the birth of components
such as that of the company’s air saving valves becomes more and
more necessary. The company offers a pressure valve in the form
Reducing
Operating
Costs
By Rethinking
Air Consumption
Riaan van Eck, SMC Pneumatics
Answering to the call of reduced consumption to not only help lower operating costs but to alleviate pressure on the country’s power is critical
in today’s manufacturing environments.
VALVES + ACTUATORS
Air saving valve
Return stroke operated
at a reduced pressure
Working and return strokes
operated at the same pressure
Working stroke
Working stroke
Flow
valve
Return stroke pressure (MPa)
Working stroke pressure (MPa)
0.9
0.7
0.5
0.3
40
30
20
10
0
0.1 0.15 0.2 0.25 0.3
Air consumption reduction ratio (%)
Pressure
valve
Return stroke
Return stroke
Conventional valve
Electricity+Control
February ‘17
32