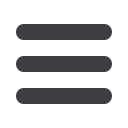

Wire & Cable ASIA – September/October 2007
55
www.read-wca.comWir & Cable ASIA – July/August 13
Traditional fibre cables allow the fibre to slide back in the
jacket enough for connectors to be attached, sometimes as
much as two millimetres. Thus, connectors were designed
with backshells that can account for the lack of additional
empty space in the cores. These connectors still conform to
GRS 326 performance levels or higher.
5 Thermal balancing
Finally, since the tape and jacket are bonded together
around the glass, thermal performance balancing was
required to enable the entire cable to perform under
standard thermal conditions. Each material – glass, tape
and jacket – has a different level of thermal coefficient of
linear expansion. This means that each material within
the cable will expand or contract at different rates under
different temperature conditions. For example, plastics
typically expand and contract up to two orders of
magnitude more than glass. In designing this new fibre,
Aramid yarn was known to have a negative coefficient of
linear expansion. But bonding everything together, most of
the effects of thermal coefficients of linear expansion were
virtually neutralised.
In the end, the cable behaves very similar to the actual
glass in terms of expansion and contraction, performing
from -40 degrees Celsius to 70 degrees Celsius with
minimal attenuation changes. Conventional plenum rated
cables typically perform from 0 degrees Celsius to 50
degrees Celsius – as required by plenum cable standards.
6 Conclusions
As optical fibre solutions evolve to areas where copper
once ruled, the importance of having the same handling,
installation and management characteristics as copper
wire cannot be underestimated. Optical cables need to
have enough strength to be pulled, twisted and cornered
similar to copper without affecting performance. By
designing new cables that eliminate air and space inside
the cable, smaller footprints can be achieved. Replacing
the loose Aramid yarns with tape wraps and bonding the
cable elements together is enabling a new evolution in
small form factor optical micro-cables. This, in turn, will
expand the available system solutions to a broader section
of customers, while providing optimal density, flexibility
and performance of fibre in enterprise applications.
7 Acknowledgments
The author would like to acknowledge the help of Ken
Nardone, Henry Rice, Bill Jacobsen and Aly Fahd in
obtaining data and test information for this paper.
This paper was presented at the IWCS symposium
November 2012.
By enabling the tape and jacket to bond as a single entity,
the fibre cable could be handled much like a piece of
copper wire in terms of strength.
While many micro-cables are available today, they
typically use Aramid yarns intertwined around the fibre.
None have actually coupled the yarns, jacket and fibre
together. This cable is unique because it uses an Aramid
tape instead of loose yarns. The tape can also be stripped
using conventional copper cable stripping machines or
copper wire stripping machines. Lineman’s scissors can
even be used to strip these cables – the first time this has
been achievable with a coated fibre without requiring a
specialised tool.
It should also be noted that RBR fibre, rapidly becoming
the standard in FTTX solutions and central offices/
data centres, also adds to the handling qualities of
these new fibres. Smaller cables can be bent around
tighter configurations to fit various types of modules and
installations.
4 Connectorisation
The bonding of the tape and jacket, however, created a
new challenge with connectorisation. Bonding the two
together eliminated the space required for the fibre to “push
back” from the connector. Therefore, connectors had to
be re-designed specifically for use with these new fibres.
These new connectors take into account that the fibre has
no push back, or compression capability, within the jacket.
1.2mm
optical
‘wire’
5lb
(2.25kg)
load
1.2mm optical
‘wire’ after
release of
pulling tension.
Note: No
deformation
24-fibre bundle,
1.2 diameter cable
24-fibre bundle,
2.0 diameter cable
❍
❍
Figure 4
: Experimental
fixture to simulate 5lb
(2.25kg) hand pull on
1.2mm patch cord
❍
❍
Figure 5
: Size comparison of 1.2mm and 2.0mm bundled cable
Minimum
normal
grip to
lift 5lb
TE Connectivity,
441 Water Street, North Bennington,
Vermont, USA
Te
l: +1 802 442 5411
:
info@te.comWebsite
:
www.te.com