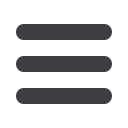

Wire & Cable ASIA – September/October 2007
53
www.read-wca.comWir & Cable ASIA – July/August 13
From optical cable to
optical wire – an
evolutionary approach
By Wayne Kachmar, Fellow, Electro-Optical Engineering, TE Connectivity, North Bennington, Vermont, USA
Abstract
This article will introduce a new design in optical fibre
cable that allows small form factor cables to have handling
characteristics that are as good or better than copper wire.
Currently, most light guides are housed in cable designs
that follow an orthodox design protocol based on one of
three basic cable types: loose tube, ribbon or tight buffer.
All require very specific handling techniques that require
special care and simply cannot be handled the same by
installers who are accustomed to handling copper.
Yet, the need for a fibre to act more like copper is
becoming more and more apparent as cable sizes
decrease and applications, such as central offices, data
centres, enterprise, and fibre-to-the home/desk (FTTH/D),
demand more fibre density. A fibre cable with the
behavioural characteristics of a copper cable will improve
installations in terms of time, flexibility and cost.
1 Introduction
Many new optical fibre cable developments have
occurred in the recent past, such as reduced bend
radius fibre (RBRF), nano-composite material fillers,
new materials for strength, connector technology, new
regulatory compliance issues (RoHS, REACH), and size/
cost constraints. During this time, cable design solutions
assumed fibre-optic cable to be a composite product
where separate elements (tight buffered fibre, aramid yarn
polymer jacket) were not bonded. Therefore, different
handling and installation requirements were mandated
based on a non-coupled core structure. In many cases,
installation stresses were overcome by sheer bulk or
material strength.
Many analogue comparisons to copper have been made
in the cable world. Other than speciality products, such
as guided torpedo fibres, no true optical analogues to
wire have been developed. Typically, cables contain one
or more insulated conductors and additional structural
elements to achieve mechanical, environmental or other
performance criteria. To date, most optical fibre designs
use a “loose core” to achieve engineered performance
in an optical cable – even single fibre cables that require
minimal protection.
The result is that many designs require installation handling
different from traditional copper cable installations. Many
failures are a direct result of installer unfamiliarity with the
special handling required by traditional indoor simplex
or duplex fibre cables. Thus, the need for a fibre to act
more like copper in terms of handling is important as fibre
adapts to use in applications where copper once was king.
There is a perception by many installers that fibre can
be handled and installed using the same methods as its
copper predecessor. However, glass is still glass, and the
performance of traditional fibre cable can still be affected
by improper handling and installation. So, why does this
perception matter?
In today’s environment, optical system solutions are being
provided to a much broader selection of customers.
Many of these installation professionals have significant
experience with copper installation practices. Yet they
are, for the most part, unfamiliar with the installation
practices of the fibre cables they are now being asked to
install. Thus, it is incumbent on fibre cable manufacturers
to educate them on acceptable handling practices. More
importantly, to improve the acceptance of optical fibre
systems in new applications, we must provide products
that will succeed under new criteria.
In terms of optical fibre cable, we must design products
that behave closer to copper insulated wire in fibre
cable handling, placement and management. New
optical waveguides have made this option viable, but
we as cablers need to continue the evolution and design
installable “cables” (wires) that meet customer needs and
define a new class of optical waveguide product.
The design presented here is a geometric core design
whereby the optical fibre is located in the centre of the core
and loose yarns have been removed in place of geometric
strength members. These strength members provide
multiple functions, such as outer jacket adhesion (to assist
with hand pulling), fibre buffering (against impact and crush
loads) and reliable access to the optical fibre for fusion
splicing or field connectorisation.
❍
❍
Figure 1
: 1.2mm vs conventional 1.6mm
1.2mm
optical ‘wire’
Aramid tape
strength
member
Conventional
1.6mm
optical patch
cord with
Aramid yarns