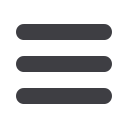

Mechanical Technology — January 2015
17
⎪
Power transmission, bearings and bushes
⎪
A
ccording to the Ernst and Young’s Global Steel Report,
2014, energy costs, excess capacity, environmental
issues and an increasingly competitive marketplace
are some of the key factors redefining the steelmaking
industry. Faced with these challenges, steel makers are modernis-
ing and revamping existing plants to improve their sector’s appeal
by improving energy efficiency and reliability; increasing spare
availability; and decreasing maintenance cost.
In an effort to increase competitiveness, ArcelorMittal has
chosen GE’s Power Conversion business to replace their existing
dc drives and control system with GE’s water-cooled Powersemi
PW100 in an important upgrade of their Bremen hot rolling mill.
“GE Power Conversion is one of the most experienced
companies in the market for modernising and revamping high
power drives for steel plants,” says Andreas Dalchow, managing
director, Hot Strip Mill at ArcelorMittal Bremen. “We know GE’s
high-performance controller (HPCi ), power electronic controller
(PECe) and its power interface board (PIBe) solutions well and
are pleased with their performance and benefits.”
ArcelorMittal, headquartered in Luxembourg, is one of the
leading steel companies in the world. The Bremen hot steel mill
is one of the largest of its kind and one of the core production
units within the group. Its strip mill currently reaches a maximum
speed of 1 300 m/min and has a production capacity of 4.5-mil-
lion metric tons per year.
The new dc drives to be provided are fitted with HPCi con-
troller technology using PECe and PIBe. This results in a freely
programmable, modular system with a real-time multi-tasking
operating system. It features modular hardware and software
and is used, in particular, for its fast information processing of
time-critical tasks in process control and related areas. It is also
used as the controller of GE’s low and medium voltage drives.
“Given the tough environment, steel makers are looking for
modern technologies that provide improved energy efficiency and
reliability, and solutions that provides a lower carbon footprint to
comply with environmental regulations,” said Mike Archibald, GE
Power Conversion’s Global Services Leader. “There is certainly
a growing need for service in this industry and GE is proud to
support our customers in all these aspects.”
The project is expected to complete by the beginning of 2017.
GE’s Power Conversion business applies the science and
systems of power conversion to help drive the electrification of
the world’s energy infrastructure by designing and delivering
advanced motor, drive and control technologies that evolve to-
day’s industrial processes for a cleaner, more productive future.
Serving specialised sectors such as energy, marine, oil and gas,
renewables and general industry, through customised solutions
and advanced technologies, GE Power Conversion partners with
customers to maximise efficiency.
GE is headquartered in Fairfield, Connecticut. In 2011, the
company was listed on Fortune 500 as the 26
th
-largest firm in
the US by gross revenue and the 14
th
most profitable.
q
GE technology increases energy
efficiency for ArcelorMittal Bremen
ArcelorMittal has selected GE’s Power Conversion
Business to upgrade the dc drives and control systems
at its Bremen hot rolling mill in Germany.