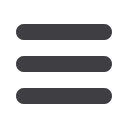

May 2015 Tube Products International
31
products & developments
Producing zero-colour,
non-oxidised weld roots
PurgExtra™ is the latest weld purging
product range from Huntingdon Fusion
Techniques (HFT) for the weld purging of
tubes and pipes from 1 to 24" diameter.
The range complements the PurgElite
®
series, but in addition has extra purge
gas inlets and corresponding exhaust
ports.
Designed for the weld purging of
titanium in particular, as well as ultra
high purity stainless steel joints,
corrosion-resistant alloy welding and
Duplex steel joints, the PurgExtra
series allows the operator to purge
normally at first, and then, when
conditions are correct, to introduce
additional gas at high flow rates to
create a faster purge and a more
efficient removal of unwanted gases.
One of the key reasons to use a
PurgExtra system is for the operator
to achieve zero-colour welds. The
extra gas flow possible with PurgExtra
models purges additional gases that
are expelled by outgassing that occurs
as the metal is being heated. The extra
gas flow will prevent these expelled
gases from combining with the hot
metal and oxidising them, which
causes the metal to discolour.
PurgExtra comprises two inflatable
dams connected by a heat-resistant,
highly flexible gas hose that has
the IntaCal
®
II gas release system
integrated. The IntaCal
®
II allows the
dams to be inflated correctly and then
releases the inert gas to safely purge
the space between the dams. IntaCal
replaces the complicated valves that
might sometimes fail and cause the
dams to burst.
The highly flexible hose allows the
PurgExtra systems to be pulled or
pushed easily around bends and elbows.
A strip of RootGlo
®
material, located
in the centre of the hoses between
the dams, allows the welder to see
clearly when the PurgExtra system
has reached the correct position in
the pipe.
RootGlo can be charged by leaving it
in daylight for 30 minutes, after which
it will provide up to 24 hours of bright
illumination inside the pipe.
Huntingdon Fusion Techniques
– UK
hft@huntingdonfusion.com www.huntingdonfusion.comPay-off and take-up stands for tubes
Queins Machines GmbH, Germany,
specialises in the manufacture of heavy
duty pay-off and take-up stands, to be
used for unwinding/winding of tubes
having a diameter between 9.5 and
50mm (
3
/
8
" to 2"). These tubes are
mainly used for manufacturing umbilical
cables in the offshore industry. The
machines are of floor-traversing type for
reel flange diameter of up to 3,600mm
(141") and reel weight up to 23 tons
(50,000 lb). Other models are being
manufactured for reel weights up to 300
tons. Further highlights are heavy-duty
belt- or chain-caterpillar capstans for
the same product, with pulling force up
to 200kN.
Queins
– Germany
info@queins.com www.queins.comStacking and bundling system
When working with round, hexagon,
squared or rectangular bars and tubes,
stacking and bundling is an involved
process. Changing from round to
hexagon bars and from one size to
another is where traditional systems
take time and manual work.
Asmag, headquatered in Scharnstein,
Austria, has developed a new
automated method. Asmag discovered
that manually adjusting the stacking
machine each time dimensions or
shapes changed was unnecessary.
Operators typically spend a few minutes
for each time they must replace inserts
to accommodate changing hexagon
bar sizes or when an insert must be
removed altogether to switch from
hexagons to rounds.
In regard to the tendency to smaller lot
sizes, this normally causes changing
the inserts once an hour. Another
disadvantage is the purchase, storage
and maintenance of the insert-sets for
each product size. The new system
eliminates that step. Usually the cams
are necessary because hexagonal
material tends to tilt at the wrong angle.
The Asmag innovation makes sure that
the bars in the first layer fall into the
right position. This system is based
on a simple idea but it has not been
used before. In addition, software
automatically calculates several
possible bundle shapes and sizes.
Asmag GmbH
– Austria
sales@asmag.at www.asmag.atSeuthe GmbH
– Germany
sales@seuthe.com www.seuthe.comHFT’s PurgExtra dam