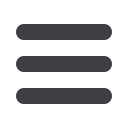

40
Mechanical Technology — November 2015
⎪
Nota bene
⎪
Index to advertisers
Afrox................................................14
Atlas Copco......................................24
Clyde Bergemann..............................31
Hytec Holdings........................OFC, OBC
Immanuel Works..............................IBC
Instruweld........................................34
Koike...............................................25
Martec.......................................13, 19
SAIW ..............................................27
SKF...................................................9
SMC Pneumatics...............................22
Tega Industries..................................23
Verder Pumps...................................33
Weir Minerals............................... IFC, 2
Industry diary
February 2016
Energy Storage 2016 Conference
3-4 February, 2016
Paris, France
mahsan@acieu.co.ukAfrica Energy Indaba 2016
15-17 February
Sandton Convention Centre,
Sandton
Debbie Mankowitz
debbie@siyenzaevents.co.za+27 82 604 5826
www.siyenza.za.comAirborne and Structure Borne
Ultrasound courses
Level 1: 17-19 February, 2016
Level 2: 22-24 February, 2016
+27 11 326 2708
matthew@martec.co.za www.martec.co.za“
F
luid power applications are
placing higher demands on a
material’s stick-slip behavior
because of the continuous quest to im-
prove performance and efficiency, while
reducing weight and lowering costs,”
says Peter Bakker, product line direc-
tor for Orkot
®
, the Trelleborg Sealing
Solutions’ proprietary composite bearing
material. “Environmentally-friendly and
explosion-safe fluids, instead of conven-
tional oils, are also more challenging
media for bearings to operate in.”
Bakker gives a typical example of
new demands from fluid power manu-
facturers. In wind turbine rotors, low
stick-slip is needed for very short sliding
movements of just a few millimeters. By
improving friction characteristics of wear
rings when adjusting the pitch of the ro-
tor, considerable energy efficiencies can
be achieved.
Wear rings are a fundamental part of
hydraulic applications and contribute to
optimising the performance of sealing
elements by transferring side loads act-
ing on the cylinder, preventing metal-to-
metal contact.
“To research wear-ring behaviour in
hydraulic applications, we specifically
design and build test rigs,” continues
Bakker. “These include machines to test
linear motion, wear-ring and counter-face
endurance and simulation of operating
conditions in temperatures and with
side loads up to the most extreme values
encountered in fluid power equipment.”
One of Trelleborg’s ongoing and exten-
sive test programmes uses a custom-built
friction and wear machine to investigate
stick-slip in reciprocating movements at
slow to high sliding speeds and radial
loads up to 50 N/mm². This research fo-
cuses on Trelleborg products such as our
Turcite
®
polytetrafluoroethylene (PTFE)
based compounds; HiMod
®
reinforced
thermoplastics and Orkot composites,
including Orkot C480.
“Turcite is the benchmark for smooth
operation of wear rings and offers the
lowest level of stick-slip,” says Bakker.
“However, load capability is limited to
10 N/mm² and composite bearings are
the option when the side loads exceed
the capabilities of PTFE.”
In tests under marginally lubricated
conditions, wear rings were installed
outside the oil chamber. Orkot composite
bearing materials perform well in low or
zero lubrication. While when tested under
a load of 40 MPa, Orkot C480 showed
extremely stable low friction – signifi-
cantly better than other composites.
“Overall, from tests so far, Orkot C480
is meeting the latest stick-slip challenges
the market is presenting,” concludes
Bakker. “We’re finding that Orkot C480
offers superior smooth sliding, either
under high side load or when held quasi-
static for extended lengths of time. That
means this latest innovation can help our
customers optimise their applications,
however high their demands.”
Orkot is a fabric-reinforced composite
material that uses thermo-set resins and
a fine weave fabric material with added
lubricants. It is good at damping vibra-
tions and operates in virtually all media.
It offers long service life, low friction and
is suitable for all commonly used counter
surfaces.
q
AWS D1.1: Structural Welding Code – Steel
a new course by Bob Shaw
The SAIW is revamping its structural steel
welding code course, AWS D1.1. The new
course is being developed by Robert Shaw,
a world leader in the field, who will be deliv-
ering the inaugural course in Johannesburg
from January 18 to 21, 2016.
Bob Shaw is founder and president of
the Steel Structures Technology Centre, Inc.,
a consulting engineering firm in Howell,
Michigan, USA. He offers 42 years’ of expe-
rience in steel construction, working seven
years with a steel fabricator, ten years with
the American Institute of Steel Construction,
and the past 25 years as a consultant.
He is a long-time active member of the
American Welding Society’s D1 Structural
Welding Committee and a member of the
AISC’s Specifications Committee. He also
serves on ISO TC167 Working Group 3,
developing a new ISO standard on the execu-
tion of steel structures.
www.saiw.co.zaAvoiding a sticky situation
Wear rings contribute to optimising the
performance of sealing elements by transferring
side loads acting on the cylinder.