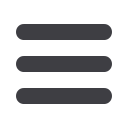

S
EPTEMBER
2012
113
12-14 November 2012
incorporating the optimum materials
and manufacturing methods to ensure
maximum performance.
Website:
www.osborn.comQuaker Chemical Corp
USA
C1852
QUAKER Chemical, a chemical supplier
to the tube and pipe industry that offers
system-wide expertise, as well as a
comprehensive portfolio of processing
fluids and coatings, has improved
production operations for customers
in welded and seamless tubular mills
worldwide.
The company was asked by a major
tube and pipe manufacturer for help with
issues it was experiencing at one of its
facilities. It had premature corrosion on
its pipes before they left the warehouse,
and the company was losing money due
to end-user warranty claims. Additive
restraints at the plant were also causing
film flow issues and the company was
experiencing low coating film builds.
Quaker’s experienced field staff
quickly identified several important
factors. Heavy mill oil on incoming
steel was impacting coating adhesion
on the pipe; gummy deposits in the
tube forming/welding operations were
causing appearance and dirt issues
on the end product; the washer the
manufacturer was using was unable
to overcome coolant issues, resulting
in marginal cleaning performance;
and vacuum issues were affecting the
coating applications.
Quaker advised the customer to
evaluate Quakercoat
®
036 UV, an
instant and UV-cured coating that
is free of VOCs (volatile organic
compounds). This custom-formulated
product eliminated the warranty claims
and gunk deposits that had plagued the
company, and gave better film builds, a
better product surface, and drier pipes.
Because the coating is more flexible, it
also met the performance expectations
of the manufacturer’s sister-mill and
expanded its client base, with improved
quality and consistency.
This tube and pipe maker now
spends less time dealing with issues
due to multiple suppliers, and Quaker
provides routine system-wide service
visits to ensure any operator questions
or concerns are addressed in a timely
manner.
Website:
www.quakerchem.comT-Drill Industries Inc
USA
C2121
PIPE and tube fabrication machinery
manufacturer T-Drill Industries, Inc has
launched the S-54 collaring machine.
The S-54 collaring system is capable
of producing tees as small as ¼" and
as large as 2
1
/
8
" in materials such as
copper, aluminium, steel, brass and
stainless steel.
The S-54 is available in versions
from a simple hand load model to a
completely automated version.
Some of the options available include
a manual feed table, or an automatic
feed table, with auto load and part
number storage.
At Fabtech the company will be
exhibiting its range of equipment for
tube and pipe fabrication, including
rotary cut-off, end-forming and spinning
machines.
Website:
www.t-drill.comXiris Automation Inc
Canada
C2312
XIRIS Automation specialises in
developing machine vision products for
the tube and pipe and metal fabrication
industries.
At Fabtech Xiris will be exhibiting the
newly enhanced XVC-O weld monitoring
camera along with the WI2000p, a
quality tool for in-line inspection of welds
on tubes and pipes.
The XVC-O weld camera can monitor
any open arc welding process used on
tube and pipe mills.
The camera combines revolutionary
sensor technology with advanced
electronics to provide a high contrast,
wide dynamic range (> 140db) image,
capable of seeing the brightest features
of a welding torch while still being able
to see the weld seam, weld pool and
surrounding darker background.
The images from the camera are
displayed on an IP54 rated HMI console
with software features that include
image post-processing, image recording
and playback.
Up to 500 hours of video can be
recorded for later review in order to
debug, troubleshoot or audit a tube
welding process.
The XVC-O features a camera module
with integrated lighting, adjustable
focus and air or liquid cooling, all
housed in a rugged enclosure able to
withstand operating in harsh welding
environments. The base package
offers a complete robust system, with
additional options such as a window
de-dusting system, and a variety of
console and camera mounts to allow the
camera to operate in a variety of hostile
environments.
The WI2000p post weld inspection
system has been developed to detect
quality issues related to the welding
process including weld undercut, sunk
welds, pinholes, weld height, weld
register (mismatch) bead roll/position
and freeze line. A high speed laser
based camera combined with fast data
capture and analysis rates provides
7µm resolution to detect weld and
forming issues independent of surface
conditions.
The process of welding tube and
pipe requires several variables to be in
check for efficient and stable production
and to meet the quality demands of the
industry.
Mill dynamics, from setup to
production, have an impact on the
stability of these variables. Measuring
and monitoring these variables is
the first step in controlling them and
improving weld quality.
Website:
www.xiris.com
WI2000p post weld inspection system
Xiris XVC-O weld monitoring camera