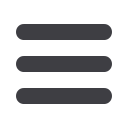

Measuring and marking
www.read-tpt.comS
eptember
2012
135
Weld camera for tube and pipe
production
DUE to the extremely bright light emitted
by an open weld arc (such as found
in a TIG, laser or plasma process),
monitoring the welding process on a
tube or pipe mill for control or tracking
of specific parameters can be a difficult
challenge. A view of the weld tip and its
immediate environment on a tube mill is
important to ensure that the weld tip is
properly aligned with the tube seam it is
welding, that the weld pool is properly
formed during the welding process, and
that a number of material inputs such as
welding wire or gas are all being fed at
ideal speeds.
To overcome the visual monitoring
challenges created by having to image a
dynamic range between the very bright
light source of the weld arc and the dark
area of its immediate environment, a
wide dynamic range camera system is
required. Typically a weld tip might be
as much as ten million times brighter
(or greater than 140db signal to noise
ratio) than the background metal area
around it. To image this is a great
challenge as most cameras today are
capable of only 60dB (about 1,000:1
dynamic range of brightness).
Cameras that are able to provide a
high contrast, wide dynamic range (>
140db) image of the weld seam, weld
pool and surrounding darker background
offer tube and pipe producers the ability
to see a number of features in their
welding process with better clarity,
providing numerous productivity, quality
and health and safety benefits for tube
and pipe production.
Xiris has developed a wide dynamic
range camera system that can be
mounted right by the welding tip to
allow the operator to remotely view the
welding process.
Wide dynamic range cameras for
weld monitoring are suitable for a
range of applications, including MIG,
MAG, TIG, plasma and laser welding,
as they provide operators with better
monitoring of inputs in the weld
environment; reduced set up time;
run time productivity; and operational
productivity.
Real time verification provides a
direct view of the welding arc and the
work environment with enough detail
for immediate adjustment, including
the ability to see the molten weld pool
solidify on a tube mill and other details
such as weld undercut, the chevrons
forming after the weld and slag and
dross contaminants forming in the pool.
Video recording provides the ability to
record, store and review vital welding
processes off line for quality assurance
monitoring, process verification and
improvement, and operator training.
Xiris Automation Inc
– Canada
Fax: +1 905 331 6661
Email:
sales@xiris.comWebsite:
www.xiris.com