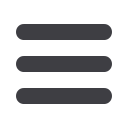

150
September 2012
Article
DNSA mill: Turks head
Repeating the alpha-gamma transformation process (alpha-
gamma transformation starts at approximately 723°C and
ends at approximately 785°C) in multi-stage annealing with
water quenching greatly improves the quality of the seam.
In order to achieve the toughness properties of the parent
metal in the weld area, the heated seam region must be
water-quenched at higher than the critical cooling rate after
annealing and then reheated above AC
3
.
The demand for higher notch impact strength can be met in
practice only with the fine grain structure achieved by double
annealing with intermediate cooling.
In inductive double annealing with water quenching after
the first annealing stage, fine carbide precipitates in a fine
crystalline matrix produce the desired favourable combination
of strength and toughness.
Hardness values above 300HV can be achieved after
normalisation. After the double annealing process, the
hardness between the inside and outside surfaces in the seam
region is approximately 180 to 200HV, which corresponds to
the hardness of the parent metal.
No yield strength loss occurs in thermo-mechanically treated
steels after induction double annealing of the seam region,
unlike the situation with furnace annealing of tubes.
Dual annealing with cooling
section
There is increasing demand for weld seam and full body
annealing to achieve homogeneous material properties.
The newly launched “Dual annealing with cooling” system
combines induction full body annealing with EloTube
TM
and
seam annealing with EloSeam
TM
.
Modern internal scraper systems with coolant return are
an essential element here. Even with tubes under 30mm in
diameter, it is now possible to reliably achieve a uniformly
annealed structure, both in the weld seam and over the
tube cross-section, with full body heating of tubes without
internal liquids. Full body heating is used for tubes with
outside diameters up to approximately 40mm, while induction
seam annealing is used for larger diameters to save energy.
EloMat
TM
converters, preferably with L-LC technology, are
used as the energy source for both annealing processes.
The dual annealing system is designed to be used with
either round coils or linear inductors with field concentrators
matched to the weld seam.
An energy source with a common cooling water system for
induction full body and seam annealing enables cost-effective
system design with a small footprint and optimal adaptation
to individual annealing requirements in the temperature
range extending from 500°C for recrystallisation annealing to
1,200°C for diffusion annealing.
Annealing processes in an inert
gas atmosphere
Inline tube annealing processes are performed in a nitrogen
atmosphere to prevent scale formation, while bright annealing
requires a reducing hydrogen/argon atmosphere.
In the manufacture of brake pipes, the tubing is sized to a
final diameter of 8.0mm, 6.35mm or 4.75mm after HF welding
at a rate of approximately 100m/min. The sized tubes are
induction annealed in a nitrogen atmosphere at temperatures
above AC
3
and subsequently chilled to below 100°C in double-
walled, water-cooled chilling tubes.
Inline bright annealing of tubes is normally used for tubes
made from austenitic stainless steels, duplex steels, nickel
alloys and titanium due to the limited welding rate of TIG and
laser welding systems (up to to 20m/min). The range of wall
thicknesses is 0.5mm to 6.0mm, especially for tube diameters
from 5.0mm to 114mm. For economic reasons, induction
annealing is no longer used for larger tube diameters due to
high gas consumption.
Inline bright annealing is integrated in continuous tube
production processes and, as an independent unit, can be
retrofitted in existing tube production lines.
Bright annealing creates a corrosion resistant seam while
retaining the bright surface of the tube. The process requires
a bright tube at the inlet of the induction zone. If necessary, a
washing unit with a tank containing a suitable, heated solution
must be used. This removes dirt, oil and grease from the tube
surface as well as dries it.
It is essential that the tube transport system keeps the tube
in equilibrium throughout the entire annealing process, ie the
same compressive and tensile forces must be present when
the tube is fed in to the heating zone and when it is removed
from the annealing and cooling zone, in order to prevent tube
compression, tapering or tearing at annealing temperatures
between 1,100°C and 1,300°C.
In the inert gas chamber, the metallic bright tube passes
through controlled induction heating and soaking zones.
Heating to the required annealing temperature takes place
in the chambers with the exclusion of oxygen and a reducing
atmosphere.
Argon, hydrogen or a mixture of these gases can be used
as inert gas. Hydrogen gas is burned off upon leaving the
chamber. Argon, an inert gas used for welding, is used inside
Weld on a longitudinally welded pipe with subsequent double-
annealing (microsection etched in order to show the ferrite line)