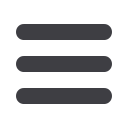

Industry News
www.read-tpt.comS
eptember
2012
45
Visitors go behind the scenes
MEMBERS of the public were given a
rare glimpse behind the scenes of one
of the world’s largest steel production
and engineering plants, and were able
to see one of the impressive 90 tonne
electric arc furnaces melt a ladle full of
steel at more than 1,600°.
Sheffield Forgemasters International
(SFIL) held a special open day to allow
guests to see what lies behind the gates
of the Brightside Lane site.
One former worker, Tony Williams,
aged 66, said he jumped at the chance
of having another look round: “I started
working here in 1961 as an apprentice
electrician when it was British Steel – I
was just 15 years old and straight out
of school. I started in the east machine
shop, which is now the scrap yard. I
wanted to come back and see how
things have altered; it’s brought back a
lot of memories. In my day there were
no hard hats, no safety glasses or ear
plugs and we had to buy our own steel-
toe capped shoes, so it’s very different
today.”
Visitors were taken on a 2½-hour tour
of the site and were able to look inside
the different areas of production, like the
forge, foundry, melt shop, the quarter-
mile-long south machine shop, and the
latest addition to the site – the north
machine shop.
Tim Hall and his 19-year-old son,
Bruce, also attended the tour and said
it was an ‘incredible day’. Mr Hall said,
“The scale of the site is unbelievable.
I run a small engineering business in
Chesterfield and so we work with a lot
of the same equipment but on a much
smaller scale.” Bruce added, “My friend
is an apprentice here and he knows
about our business so we wanted to
learn more about his place of work. It’s
good to see there is still some British
industry leading the way.”
Also in attendance were The Bentley
Drivers Club; a father and son who
travelled from Wiltshire; and BT
apprentices. Mark Tomlinson, technical
director of the melt shop, said, “We
started running the annual open day
five years ago and it has increased in
popularity. We get so many requests
from people wanting to look around
the site and see what we do that we
decided to hold a day-long event that
gave people that chance. It’s also a
really good opportunity for employees’
friends and families to understand more
about what happens when their loved
one heads off to work.”
Sheffield Forgemasters
International Ltd
– UK
Fax: +44 114 251 9013
Email:
sales@sfel.comWebsite:
www.sheffieldforgemasters.comTo achieve perfection in your finished drawn tubes, you
need to start with precision tube hollows. And that means
starting and ending at
Tube Hollows International
.
No one else matches our ability to provide high quality,
uniform wall thickness hollows…to meet your specs exactly.
•
Wall thickness tolerances to ±1%
•
All commercial and medical alloys
•
Tube conditioning — improves surface finishes and
concentricity
•
Deep hole drilling, trepanning, honing, grinding and
turning
•
We serve a range of industries:
medical, aerospace,
oil & gas, nuclear and automotive
Contact us today for a free quote or to discuss your needs:
207.935.8823 •
info@tubehollows.com395 Portland Street, PO Box 160, Fryeburg, ME 04037 USA
T
1.207.935.8823 •
F
1.207.935.8824 • TubeHollows.com
For perfect
finished
tubes,
start
with
the world leader in seamless precision:
Tube Hollows InTernaTIonal
Visitors take their hats off to the open day