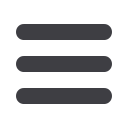

Technology News
www.read-tpt.com54
S
eptember
2012
Gräbener Maschinentechnik
offers the entire value chain
TRADITIONAL hydroforming is currently
experiencing a renaissance. More and
more companies rely on hydroforming
technology, yet there are only a few
machine builders left in this sector. In
contrast to the other machine builders,
Gräbener Maschinentechnik GmbH
& Co KG (GMT) offers the entire
value chain of hydroforming: from the
customer’s general idea, the simulation,
the resulting engineering and prototyping
respectively small series production up
to the customised press.
From the very start, GMT has been
designing the hydroforming presses
based on and customised for the
individual component of the customer.
For example in 2002, the RoboClamp
®
,
the world’s most powerful hydroforming
press with a closing force of 13,000
tons, was perfectly and completely
tailored to the component to be
manufactured – a vehicle side rail. This
engineering approach has always been
and still is the philosophy of Gräbener
Maschinentechnik.
The patented Powerboxx
®
with a
closing force of 6,500 tons is yet another
in-house development of GMT for the
production of separator plates for fuel
cells. With the Powerboxx
®
, the closing
force can be concentrated on a small
surface of 300 x 200mm.
In addition to this, GMT conducts
feasibility
studies
and
forming
simulations. For the design and
engineering of hydroforming presses
and the corresponding tools, GMT
applies most modern software such
as CATIA V5, Inventor, mechanical
desktop. The program FEM Tool Ansys
is used for the FEA analysis which is an
integral part of the engineering.
When purchasing the former
Schuler premises in Wilnsdorf
(“Schuler Hydroforming”), the
Graebener Group also took over
three hydroforming presses. With
a total of five presses available
today, GMT can test innovations
and in-house developments for the
sector of ‘Prototyping/Small Series
Production’ at short notice using
its own machinery. Presses with
closing forces of 400, 2,500 and
10,000 tons have been added to
the already existing presses with
closing forces of 1,500 and 6,500 tons.
Thus, Gräbener should be in possession
of the world’s largest number of
prototyping presses.
The 1,500 and 6,500 ton presses are
already booked solid. The 1,500 ton
press is used continuously by customers
for the prototyping and the production
of parts in small and medium lot sizes.
The 6,500 ton press is used throughout
the entire year in order to meet the ever
increasing demand for metallic separator
plates for fuel cell production.
The 2,500 ton hydroforming press is
also used for further enhancing the open
and thus highly flexible control program
PressPro
®
developed by Gräbener.
The 10,000 ton press, which is also
the hydroforming press with the world’s
largest table surface (6,000 x 2,200mm),
is currently being overhauled in order to
be ready for prototyping purposes with
multiple tools.
These exceptional machine capacities
enable Gräbener Maschinentechnik to
offer tailor-made machine concepts to its
customers: From four-column presses,
frame presses, C-frame presses such
as the RoboClamp
®
to the PowerBoxx
®
or the PowerTower
®
for the production of
hydroformed plates.
Gräbener Maschinentechnik GmbH
– Germany
Website:
www.graebener-maschinentechnik.deTransforming tubes technology
SINCE GFU was founded in 1989, the
owner-managed company has evolved
into a worldwide specialist for plant
technologies in transforming tubes.
Engineering and manufacturing of
upsetting presses, swaging presses,
high speed end forming units, neck down
machines, expanding and reducing
machines and also forging machines
belong to the current scope of delivery.
OCTG industries took attention of the
upsetting and swaging technologies
made by GFU to manufacture tubing
casings and drill pipes. Automobile
industries use the GFU upsetting
technologies to produce tube camshafts,
sway bars, drive shafts and others.
High speed end forming is also used
for automobile applications. High-
pressure airbag vessels and shock
absorbers made on GFU end forming
machines can be found in millions of cars
worldwide. This technology also finds a
place in manufacturing flanged shafts,
conveyor rollers, pressure accumulators,
extinguishers and gas tanks.
Applications like shock absorber
tubes or high-pressure airbag vessels
are manufactured with combined
processes. GFU engineers find solutions
to bring these combined processes in-
line. Production plants engineered by
GFU are built in modular configuration
to enable customers to complete parts
right up to ready machined, cleaned and
measured parts. Solutions with combined
GFU processes like upsetting and end
forming can be found in one production
line. Pyrometers and measurement units
are mostly involved to create safe and
stable processes.
GFU GmbH
– Germany
Email:
info@gfu-forming.deWebsite:
www.gfu-forming.deTailor made machine concepts