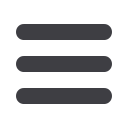

72
S
eptember
2012
Technology News
Schuler offers turn-key plants for efficient produc-
tion of large pipes.
Efficient, flexible and reliable.
• Presses for longitudinal welded pipes
• Spiral pipe welding machines
With Schuler you have strong support in R&D,
engineering, large-scale system construction,
project management and global service.
Forming the Future
Schuler Pressen GmbH
|
Bahnhofstr. 41
|
73033 Göppingen
Germany
|
Phone +49 7161 66-307
|
Fax +49 7161 66-729
largepipes@schulergroup.com|
www.schulergroup.comMaking the Earth’s arteries.
Production systems for large pipes.
Visit us at Tube India
Hall 1, Stand 1G10 / 1H11 | Mumbai, India
30 October – 1 November 2012
AMEMBEROFTHE
SCHULERGROUP
AZ_Largepipes_2b_87x260_Atis_Tube_India.indd 1
26.07.12 14:17
Surface crack
detection
system
THE ISOTEST 30 E mobile crack detection unit is a new,
state-of-the-art power pack designed by Magnaflux GmbH
of Essingen, Germany for magnetising specimens with AC
or full-wave DC in magnetic powder testing. Satisfying a
requirement expressed by numerous customers, this system
complements the company’s range of Isotest mobile systems
60E (for test currents up to 6,000 A DC) and 100 E (for test
currents up to 10,000 A DC) with a model designed for test
currents up to 3,000 A DC and AC. The model 30 E features
a new, wear-free electronic high-current change-over switch,
which enables easy and quick switching between DC and
AC with the simple push of a button, without the need for re-
connecting or re-assembling high-current cables.
This light-weight and extremely compact power pack
provides exceptional mobility and flexibility on-site. Isotest 30
E is suitable for use in all industries where highest reliability
under harsh conditions is a requirement, including the
automotive and aeronautical industries, foundries, forging
shops, steel production and processing, along with OEMs
and suppliers, testing contractors and service providers.
All three Isotest models enable the demagnetisation of
work pieces previously magnetised with full-wave DC current
by means of a multi-stage, low-frequency demagnetisation
system. The control system is programmed in such a way that
current control starts at least with the selected test current
intensity and is then continued until zero current is reached.
This ensures the complete demagnetisation of the work
piece, as is required for many of the subsequent processing
steps. Alternatively – depending on the type of magnetisation
selected previously – demagnetisation with alternating
current is also possible. To increase testing safety, the
Isotest systems, which are designed for constant current
magnetisation or impulse current magnetisation, feature a
constant current control or (optional) current flow detection
system. A broad spectrum of high-current cables, coils of
various diameters and designs, and a variety of contacting
options provides the user with maximum flexibility.
Holger Wilhelm, head of sales office and service at
Magnaflux, Germany, commented: “In the design of the
new Isotest 30 E system, we were guided strictly by market
requirements. We are offering a system that provides a
maximum of operator convenience, safety and mobility,
with a combination of features which is, to our knowledge,
currently unsurpassed anywhere in the world. Our customers
can now choose exactly the performance level that best suits
their requirements. In addition to our three mobile standard
crack detection systems, we also offer stationary systems for
testing large work pieces, as well as customised designs – for
example, we have built several systems with test currents up
to 3x17,000 A for multidirectional testing.”
Magnaflux GmbH
– Germany
Email:
info@tiede.deWebsite:
www.tiede.de