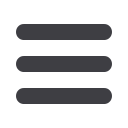

News
Corporate
September 2015
12
www.read-eurowire.comWire and Plastic Machinery has recently
acquired wire and cable manufacturing
equipment, which is still installed in the
western USA. The equipment is being
offered for immediate sale.
Highlights include:
•
Northampton 1.8m (1995) and 1.25m
(1994) double twist bunchers
•
MGS 1.25m double twist buncher
(1995)
•
Syncro FX-13 rod breakdown machine
400HP DC, F annealer, 30" (760mm)
dual spooler
•
CWF rod breakdown 8mm–1.6mm,
13 die, F annealer, Bongard 1,050mm
drop coiler (1999)
•
560mm
(22")
Watson
37-wire
6+12+18 rigid strander. AC vector
motors and drives
•
560mm
(22")
Watson
61-wire,
6+12+18+24 rigid strander. AC vector
motors and drives
•
Two 4½" (114mm) Davis Standard
24L/D sheathing lines
•
Two Skaltek MP-360 coiling lines
•
600mm Merritt Davis dual spooler
Others include 1.2m Edmands and
760/630mm
Lesmo
DT
bunchers,
1.5m/1.8m MGS rewind line.
Wire & Plastic Machinery Corp – USA
Website
:
www.wireandplastic.comEquipment still
installed
Developing and refining
▲
▲
Northampton 1.8m double twist buncher, made in
1995
Since 1969 Clifford Welding Systems has been developing and refining its range of
mesh welding machines for the production of welded wire reinforcing mesh, welded
wire fine mesh, welded wire mine mesh, welded wire fencing mesh and other welded
wire mesh products.
Successfully manufacturing a machine that can produce these products efficiently
and reliably is the result of many years of development and world-class engineering
expertise.
An example of Clifford’s capability and one of the most successful mesh welders is the
quick-setup Engineering mesh welder. This machine can accommodate a wide range
mesh spacings, commonly multiples of 2" and 3", without having to move any of the
linewire or welding elements, resulting in no setup time for this portion of the machine,
and a radically reduced change over time when switching products.
Businesses are now able to efficiently and cost effectively produce an order for a
customer of a single panel of mesh, and some customers have reported being able to
do up to 20 mesh style changeovers in a single shift.
Clifford has also been successful in the production of efficient and highly productive
mine mesh welders. The most critical requirements of high quality mine mesh are
a consistent and high strength weld and a dimensionally accurate piece of mesh in
length width and squareness.
Achieving these high quality requirements on a consistent basis thousands of times
a day is no small feat, and requires very precise and finely tuned machines. Clifford’s
mine mesh welders use an absolute positioning system and a double pullout system to
ensure consistent accuracy and high levels of production efficiency.
In order to ensure the best quality weld with the highest weld strength Clifford uses
a single point welding element narrow enough to include a single weldpress and
transformer for each weld intersection; each element is controlled by a separate weld
controller that utilises positive current feedback to accurately measure and adjust the
current in each weld intersection. This ensures it can reliably produce a consistent weld
quality, dramatically reducing costly re-work and product returns from customers.
Clifford’s mesh welders are modular in design and can be equipped with many
accessories, including manual and automated feeders for introducing the linewires into
the welding portal, semi-automatic and fully automatic turning and stacking systems to
remove the welded panels from the welder, mesh stack tying stations, bundle stacking
systems, automated weighing stations, conveyor systems and tagging stations.
The company has, this year, opened new dedicated sales and service offices in the USA
and Dubai, and appointed new distributors throughout Asia. The company is also in the
final stages of development of some new revolutionary products.
CliffordWelding Systems (Pty) Ltd – South Africa Website
:
www.cliffeng.comDavis-Standard LLC has appointed James
Murphy as president and chief executive
officer. Mr Murphy has been an integral
part of Davis-Standard for more than
25 years, progressing through various
leadership roles in sales and engineering
management.
He is also one of the most respected and
active leaders in the plastics industry, most
recently serving as chairman of NPE 2015.
Prior to this promotion, Mr Murphy was a
member of Davis-Standard’s office of the
president and responsible for leading the
company’s sales and marketing efforts.
In his new role, he will be supported by
a strong leadership team in the United
States, Europe and Asia.
“I am honoured by the opportunity
to lead Davis-Standard and excited
about our future,” said Mr Murphy. “The
Davis-Standard family is almost 900
strong and working around the clock
to serve customers worldwide. We
are a market leader with outstanding
employees and industry partners. We
will continue to work together to build
stronger customer relationships, cutting
edge technology, and superior service
and support.”
Robert Geckle, a current member of
Davis-Standard’s board, will support
the leadership team as chairman. Mr
Geckle has been part of the board
of directors for over a year and has
significant executive experience with
industrial companies and private equity.
His most recent corporate position was
as president of the Textron Fluid and
Power Systems Group. Prior to that, he
was president of Branson Ultrasonics,
the market leader in plastic joining
technology.
Davis-Standard LLC – USA
Website
:
www.davis-standard.comNew president and CEO for Davis-Standard