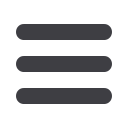

90
S
eptember
2015
Global Marketplace
Steel
With its embrace of a scrap-based
process, US Steel takes example
of Nucor – but the minimill’s
culture is something else
altogether
“If you can’t beat ’em, join ’em. The granddaddy of old-
fashioned steel companies is now saying it needs more
variable production.”
The “granddaddy” invoked by Deutsche Bank analyst Jorge
Beristain is US Steel; and the company it failed to beat and
is now imitating, under the impetus of a global steel glut, is
Nucor. Other steel industry observers consulted by the
Wall
Street Journal
expressed similar views of the two companies
– the only US-based steelmakers still among the top 50 steel
producers worldwide. That list is now dominated by Chinese
companies. (“Steel Firms in US Strive to Cope with Imports,”
17 June)
In the opinion of the
WSJ
’s Pittsburgh-based reporter John
W Miller, the construction by US Steel of its first electric
arc furnace in decades signals a major shift in American
steelmaking. The company has begun dismantling the stable
of iron-ore-reliant blast furnaces at its World War I-era mill in
Fairfield, Alabama, near Birmingham, and will install a scrap-
based process that allows for stopping and starting production
when there is not enough demand to keep churning out steel.
The name Nucor, of course, instantly suggests scrap.
“Just over an hour’s drive away [from Fairfield], in Decatur,”
Mr Miller wrote, “Nucor Corp has been turning old cars and
refrigerators into fresh batches of steel for more than a
decade, with two electric arc furnaces and a flexible, non-
union workforce.” Those methods helped Nucor (Charlotte,
North Carolina) overtake US Steel last year to become
America’s biggest steelmaker by production capacity.
Mario Longhi, the US Steel CEO, who took the job almost two
years ago, admires the Nucor approach but thinks it can be
improved upon. In building the new Birmingham furnace, he
told the
WSJ
, “We want to be more flexible than Nucor.”
But if it is to adapt any part of the Nucor model to its own
purposes, the 114-year-old Pittsburgh company must first
meet and overcome a major challenge. US Steel’s workers
are unionised. Nucor’s are not.
T
he
appeal
of
a
non
-
union
shop
Writing in mid-June, when US Steel’s 2,100-strong work force
was anxiously monitoring contract talks between the company
and the United Steelworkers, Mr Miller pointed out why the
union labour issue is central to any makeover. Some 2,500 US
Steel workers were currently laid off. Nucor has an unofficial
no-layoff policy. US Steel has lost money in five of the last six
years. Nucor has been consistently profitable.
For US Steel, with over $2 billion in pension liabilities and tens
of thousands of blue-collar workers making between $50,000
and $150,000 a year, the stakes were high in the first contract
bargained during a down market since the early 2000s. In this
context, union leaders sensed that Nucor’s non-union shop
was as much an attraction for Mr Longhi as its steelmaking
methods.
›
Taking a closer look at Nucor, which assumed its current
form in 1972, Mr Miller noted that its Alabama plant
produces roughly the same amount of steel as US Steel, 2.4
million tons per year, but employs about one-third as many
workers. “Managers and workers emphasise their unique
brand of steelmaking,” he wrote. “Employees call one another
teammates and talk up their competitiveness.”
Expressing a company preference for “can-do, innovative
guys”, plant manager Mike Lee told Mr Miller that “athletes
or military” account for a high percentage of hires. With each
batch of steel they make, workers get a scorecard assessing
their performance. An incentive-based pay structure means
that salaries range from over $100,000 to less than half that.
The Nucor culture would seem to promote morale, with
workers coming to the mill to clean or do research during
downtime. Techniques developed during a shutdown in 2009
helped the company become more productive when the mill
started pumping out steel again, said Mr Lee.
In contrast, wrote Mr Miller, “There aren’t many mills more old-
school than US Steel’s Alabama plant.”
›
Meanwhile, as construction of the new $230 million
electric arc furnace goes forward at Birmingham, US Steel
workers at mid-year were not yet fully trained in its operation.
“We’re trying to find a facility with an EAF, but most of the EAF
facilities are non-union so they’ll let company officials visit but
not us,” union local president David Clark told the
WSJ
. “We
do know our scrapyard is going to be 20 times the size it is
now.”
In the end “I think [Mr Longhi] is going to succeed,” said union
trading coordinator Fred Gipson. “But a lot of us are going to
suffer.”
An unintended consequence of
sanctions: cheap Russian exports
of finished steel and scrap ‘wreak
havoc’ in the American market
“Over the past six months Russian scrap and finished steel
products have flooded the US market thanks to the attraction
of earning high-value dollars for a product with a rouble cost
base.”
On 2 June,
Forbes
contributor Tim Treadgold was pointing out
an irony in the American and European economic measures
taken against Russia after the Ukraine incursion: together with
lower oil prices, due in part to higher US oil production, the
sanctions that have shrunk the value of the Russian currency