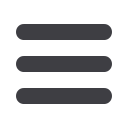

4
AN EFFICIENT AND RESPONSIBLE GROUP
3. A Group that is committed to the professional growth of its employees
80
SAINT-GOBAIN
- REGISTRATION DOCUMENT 2016
A Group that is committed to the
3.
professional growth of its employees
THE HEALTH AND SAFETY POLICY
3.1
Health and safety are central values at Saint-Gobain in the
management of its industrial, distribution and research
activities. They stem from a strong desire, from the company,
strengthened by the commitment of employee.
(OHSAS 18001 – ILO-OSH 2001) was 365 at the December 31,
2016 against 364 in 2015 at constant perimeter.
The number of sites certified for health and safety
subcontractors will also be taken into account.
With regard to safety, the TRAR indicator is the total
recordable accident rate for one million hours worked by
permanent and temporary employees. As from January 1,
2017, recordable accidents and hours worked by permanent
Delegation must draw up and apply action plans for the
implementation of the Group’s Health Policy following
consultation with the Sectors and Activities.
With regard to health, the Group’s objectives for occupational
risks concern toxic agents (including crystalline silica and
dust), noise, ergonomics and psychosocial risks. Each General
A health and safety risk assessment
3.1.1
Saint-Gobain bases its health and safety management on the
identification, reduction and control of occupational risks.
to noise (NOS – NOise Standard) and the standard on toxic
agents (TAS - Toxic Agents Standard) (see chapter 3,
section 6.1.3).
standard developed in 2013. This standard defines the
process to be followed to identify dangers and to analyze the
potential health and safety risks. It refers to specific health
risk assessment standards, such as the standard on exposure
and safety risks has been applied by the Group’s EHS
Department. It aims to guarantee its identical and consistent
implementation throughout the world, in accordance with the
Since 2014, a training program on the evaluation of health
Group site will have a guarantor capable of leading the
prevention measure according to the method and of ensuring
that the processes comply with the Group standards.
applies the method defined by the Group. In future, each
been trained or certified in each General Delegation. These
delegates ensure that the local EHS network is trained and
One or more delegates to the risk assessment method have
Based on the health and safety risk assessments made, the
the consequences and deal with the effects thereof).
sites define the priorities and the action plans to be
implemented in order to best control these risks. Risk
prevention applies at 3 levels: primary (avoid or eliminate
exposure), secondary (deal with the risks) and tertiary (limit
Safety, a central value to the Group
3.1.2
Everyone's responsibility
a)
subcontractors, safe conditions and a safe working
environment, beyond the requirements of the applicable local
legislation.
Employees’ safety, in the same way as health, is a priority at
all times for the Group with a single acceptable objective:
zero work-related accidents. Saint-Gobain aims to ensure for
all persons on its sites, including temporary workers and
in his own safety and in that of his colleague.
endeavors to place safety at the heart of the corporate
culture. Safety is a value held by all management grades and
by all employees. The objective is that everyone participates
This measure affects all the Group’s businesses and
results and the resources invested, particularly by carrying
out safety inspections and by applying safety standards.
everywhere and guarantees all aspects of safety: objectives,
action plans and performance measurement. To emphasize
this commitment, a portion of the managers is based on the
At the highest level, the management has demonstrated its
involvement in the development of a culture of safety within
the Group. The operational management is responsible
which represents a ratio of 2.73 inspections per employee
and temporary worker.
478,545 SMAT inspections were made within the Group,
conditions, which form the subject of an immediate priority
action or an action incorporated into an action plan. In 2016
aim to encourage open dialogue with the person visited, on
the subject of safety (and health), following the observance
of work practices by the inspector. The positive points are
noted as a priority, as well as any dangerous acts or
Safety inspections are organized on all sites according to the
SMAT (Safety Management Tool) standard. These inspections