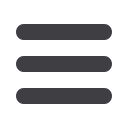

1. Introduction
Best in Class companies worldwide, defined as such for their high percentage of Overall Equipment
Effectiveness (OEE) and low injury frequency rate; continue to show strong initiatives intended to expand the
safety of their operation. From executive sponsored programs at the corporate level to the definition of proactive
risk management strategies, these companies are investing in safety systems and processes; simply because in
most cases, safety is identified among the core values of those companies, at the center of their production
process and among their key performance metrics, closely linked to their productivity.
There are numerous publications and records of Industrial Accidents, a large number of them with terrible
consequences, including not only loss of human life or environmental impact but also affecting the production
assets in the site. As an example, in researching for this paper, the authors found record of at least 20 “notable”
oil and gas offshore blowouts between 1980 and 2010.
For this paper, the authors compared two serious incidents in the Oil & Gas sector; Piper Alpha operated by
Occidental Petroleum and Deep Water Horizon leased to BP. Although both incidents are 22 years apart from
each other and occurred in different geographies and have many differences in causes and consequences,
each incident illustrates the risk and the potentially catastrophic dimension this industry must confront and the
impact on people, environment and corporations, which might cease to exist after these incidents.
2. Defining Safety and Risk
Safety is defined in the industry as a reduction of existing risk to a tolerable or manageable level while risk is a
combination of the probability of a harmful incident and magnitude of the harm.
Traditional design practices allocate the risk reduction across different and independent protection layers. The
rationale behind it is simple “any system that can fail will fail” so the engineering best practice is to distribute the
risk reduction tasks across multiple independent functions or systems. One of these systems is a Safety
Instrumented System.
2.1. Safety Instrumented Systems one of many Independent Protection Layers to Reduce Risk
A Safety Instrumented Systems (SIS) is a mission critical system designed following international design
practices such as IEC61508 [1] Functional Safety Standard to reduce risk to the people in and around the
production environment, the environment, the production asset and the business. In many cases the Safety
Instrumented Systems are the last resource to prevent disaster.
SIS performance is measured by Safety Integrity Level (SIL) SIL 1 low, SIL 3 high or Risk Reduction Factor.
As mentioned earlier, the Safety Instrumented System is one of many functionally independent systems each
intended to perform a task, as shown on Table 1 typically referred to as Independent Protection layers [2]