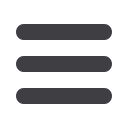

1.5. How is a compliant O&M FSMS developed within the End User and Supply Chain?
A Functional Safety Management System (FSMS) is usually developed as a result of a gap analysis
performed against the existing in-house company ISO9001 Quality Management System (QMS), and
the requirements of the relevant clauses of the good practice safety related standards; IEC 61508, IEC
61511 and ISA84 and also any supporting standards dependent on SIS scope i.e. IEC 62061 and IEC
61800-5 for machinery. Most organisations will purport to have the QMS certification as the baseline of
a structured procedural approach to try and manage functional safety within them; however experience
suggests that the process of a detailed gap analysis of these ‘Hybrid’ systems usually identifies that
many of the recommended techniques and measures required by the standards are generally missing,
or are inadequate.
For the Asset Operator, it will be important to assess the capabilities of both the internal O&M systems
as well as the supply chain to deliver a comprehensive documented solution to meet industry and
regulatory good practice expectations.
From experience of assessing many FSMS over time, the inclusion of simple high level ‘additions’ to
QMS systems that have little substance behind them does not provide adherence to the normative
requirements of the safety standards. In particular, the procedures become weaker in detail and
competency requirements when greater levels of risk reduction are required to be engineered e.g. SIL
2 and above.
Responsible suppliers who embrace the ‘best in class’ requirement of their clients, will go to great
lengths to both interpret and provide terminology understanding of the relevant safety related standards
(and how this relates to the existing QMS process) for the development of an additional FSMS
procedural set which results on the existing QMS being extended and improved.
Such commitment to FSMS development by the supplier requires extensive internal resource and
funding and requires continual effort to maintain its relevance once developed. Similarly the SIS design
engineering, operations and maintenance documentation and verification and validation activities
delivered by these best in class organisations will differ to that of a typical non-safety related projected.
It therefore follows that Asset Operators seeking to partner with a responsible supplier will expect to
see the provision of FSMS compliance activities within any proposals receipted against a safety related
bid enquiry.
This attainment of a robust methodology to demonstrate that functional safety is being managed
correctly should be a key recognition factor for Asset Owners and EPC’s as a means to underpin their
own FSMS requirements. By doing so this provides increasing confidence and assurance that SIS
solutions that are being developed on their behalf are satisfactory.
Such supplier FSMS commitment ultimately demonstrates to the Asset Owner that the supplier:-
Ø
Provides documented and traceable compliance to the Industry good practice safety standards
Ø
In use and continuous improvement of the FSMS, allows the supplier to work closely with the
Asset Owner/EPC to ensure that functional safety management is executed to provide safe and
reliable solutions drawing on the combined experience of the Asset Owner/EPC and supplier
project teams