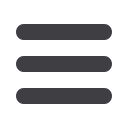

Ø
Ensures that the FSMS is fit for purpose and withstands detailed stakeholder scrutiny / audit
and is underpinned further by appropriate third party assessment
Ø
Ensures that the safety elements engineered for the solution meet the requirements of the
standards in terms of functionality and reliability e.g. ABB’s 800xA Hi SIL 3 capable safety
controller
1.6. So are all FSMS Procedures the Same?
As with all supplier claims to competency and procedure / systems that are deployed to design and
engineer SIS solutions, the depth and rigour for key compliance requirements can vary greatly.
There is a stark difference between a self-declaration of conformity to IEC 61508 / IEC 61511 and an
accredited third party certificate from a leading Industry certification body such as TüV. The
effectiveness of any O&M FSMS can only be measured on the basis of the third party certification audit
to ensure it complies with the requirements of the safety standards. When it comes to the Asset
Owner/EPC making a selection on a supplier to design, engineer and verify the adequacy of a SIS
solution it follows that suppliers who have gone the extra mile effectively differentiate themselves from
the competition.
As the ultimate responsibility for functional safety management (FSMS) resides with the Asset Owner,
then clearly a professional and compliant approach to the development of the system utilising an
accredited FSMS methodology represents ‘best in class’ management of the functional safety
requirements. This allows traceability and transparency for FS requirements to be audited and
assessed by both in-company and regulatory stakeholders alike.
Likewise, the reciprocal to this approach for a solution developed by a less robust FSMS could lead to
the potential for:-
Ø
Misinterpretation of ITT technical solution responses by the project owners commercial team
during cost comparison analysis of response content
Ø
Project schedule slippages, due to time spent in clarifying TQs & PQs, performing impact
analysis and in-depth verification and validation for every change in the specification i.e. design
by TQ
Ø
Potential for expensive re-engineering of the solution at factory acceptance testing (FAT) based
on misinterpretation of requirements and poor functional safety management practices
regarding baseline assumptions and technical application, which invariably impacts on
resources and costs
Ø
The potential that a safety system that does not meet the necessary risk reduction could be
installed at site
Ø
Lack of demonstrable traceability to Industry good practice standards
Ø
Potential exposure to liabilities both corporately and professionally
Ø
Failure to recognise the asset management ‘inherent benefits’ of the technology solution offered
i.e. use of ABB 800xA asset management diagnostics features