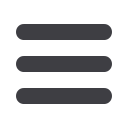

Technology
News
41
Wire & Cable ASIA – March/April 2007
Accuracy is the name
of the game
A laser scanning system with an
accuracy of ±0.1mm has been
developed by American company,
Laser Design Inc.
The
PM-300
Extrusion
Profile
Monitoring System, monitors extrusion
profiles in real-time.
Already installed at a major US window
manufacturing company, the system
automated their manual measuring
process that previously stopped
production lines, costing them millions
in lost revenue.
The PM-300 system’s three laser
probes monitor the two-dimensional
cross-sectional profile of moulded vinyl
and wooden products used in window
frame construction.
The PM-300 is the first low-cost
complex profile monitoring system with
exceptional ±0.01mm accuracy.
It checks multiple complex feature
measurements at the rate of 12
times per second on inline extrusion
production lines.
The continuous monitoring happens
in real-time during the manufacturing
process, so every extruded portion
is verified. Corrections can be made
right away whenever the ongoing
measurements indicate a problem.
When thousands of parts come off the
line per day, the cost and time savings
potential is enormous.
Laser Design markets the PM-300
system worldwide. “Our Extrusion
Profile Monitoring System is affordable
for all types of extrusion scanning
applications, both large and small,”
said C Martin Schuster, president of
Laser Design.
“Window rail component manufacturing
is a good example of where this system
can replace the time-consuming,
off-line periodic sampling process
that stops the production line with
uninterrupted
non-contact
profile
monitoring using our laser scanners.
“Productivity is greatly increased and
accuracy is continuously monitored by
the PM-300 system.”
When profiles are monitored on a non-
stop basis, any deviations from spec
are caught immediately and corrected,
before the production line makes
hundreds of faulty products.
“This technology is perfect for
monitoring extrusions of aluminium,
wood, vinyl, vinyl-clad, and rolled steel
shapes,” Schuster added.
“The PM-300 system’s successful
implementation
in
the
window
manufacturing industry is just one
example of the many industries that
could benefit from the technology.”
Laser Design Inc – USA
Fax
: +1 952 884 9653
:
sales@laserdesign.comWebsite
:
www.laserdesign.comThe new PM-300 laser scanning system
▲
Dry cleaning – Decalub
style!
Decalub, France, has introduced
its new dry cleaning, coating and
drawing (DCCD) process, greatly
improving the present state of rod
preparation, wire lubrication, and
in-line wire cleaning.
The process allows immediate
substantial cost savings in drawing
applications, including spring wire,
high-tensile rope wire, bead wire,
PC strand wire, galvanised H/C or
L/C wire, AL cladded wire, plating
wire, CO
2
welding wire, colleted nail
wire and cold heading wire.
All those products are drawn directly
from mechanically descaled bare
rod containing up to 0.88-0.90%C,
at the highest drawing speeds,
without traditional wet pre-coating
chemicals, in a completely dry, one-
step operation.
The DCCD process incorporates
high-performance
rod
acid-free
preparation and dry coating/
lubrication technology, enabling
‘frictionless’ drawing with the full
lubricant film at wire-die interface
(physical separation of metal-to-metal
contact), thanks to an automatically
controlled fusion of the standard
lubrication compounds.
Such a liquefied substance, with
controlled viscosity, performs an
exceptionally consistent residual coat,
adjustable in weight at all speeds,
eliminating the need for phosphate
and borax pre-coating chemicals and
their wet substitutes.
Full film coatings are achieved
automatically in a wide variety, from
ultra thin for plating wire through a
strongly adherent hard coat for spring
wire and similar products.
One of the system’s new applications
consists of direct drawing of
mechanically descaled H/C rod,
without pre-coating chemicals, with
water soluble sodium lubricants in all
drafts, enabling in-line wire cleaning
for wire plating, galvanising, brass
coating, etc.
The
DCCD
process
features
‘zero’ energy consumption, ‘zero’
consumables cost and is easy to
operate (fully automatic) and very
simple to install in-line with any wire
drawing machine.
There are no hot liquid tanks for
rod pre-coating, no hot air blowers
to dry wet rod and, therefore, the
process operates at virtually ‘zero’
maintenance cost.
Decalub – France
Fax
: +33 1 60 20 20 21
:
info@decalub.comWebsite
:
www.decalub.comAcid-free rod cleaning and wire drawing
▲