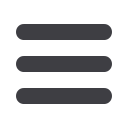

Technology
News
43
Wire & Cable ASIA – March/April 2007
Increasing capacity 10-fold
The capacity of FisherTech’s Injected Metal Assembly (IMA™) process has
been increased 10-fold with the launch of the AM51 system.
A maximum shot volume of
up to 500 grammes allows
for forming and joining of
much larger component
assemblies
and
end
terminations.
New design features, such
as a stationary operating
head, shot control and a
two-stage melt pot, provide
options for advanced auto-
mation up to full robotic
operation. Pneumatic injec-
tion increases operating
capability by 50% for
greater productivity, re-
duced operating costs and
improved die cast integrity.
IMA technology uses molten
zinc alloy to die cast a component while it is simultaneously joined to other
components in an assembly, or to form and join an end termination directly
onto a wire, cable, rod or shaft.
This process eliminates one or more pre-manufactured parts from the
assembly, as well as multiple joining methods for increased cost saving.
The precision die casting tool ensures high quality, close tolerance part-to-
part consistency with no secondary finishing required. The zinc alloy, with
mechanical properties equivalent to low carbon steel, forms a high strength
component, and the alloy’s fluidity allows casting of complex, intricate detail.
FisherTech – USA Fax
: +1 705 748 6312
:
info@fishertech.comWebsite
:
www.fishertech.comFisherTech’s new AM51 system
▲
Latest addition to the USYS
family from Zumbach
Zumbach Electronics has introduced
the latest version of their well-proven
multi-tasking controllers of the USYS
family.
The new model USYS 200 reflects many
new features and improvements for
comprehensive on-line measurement,
control and quality monitoring.
USYS 200 is a complete system for
one measuring point (1 diameter/
ovality gauge ODAC or 1 eccentricity/
diameter gauge ODEX or 1 capacitance
measuring system CAPAC).
Additional sensors for faults, events
and line speed can also be connected.
A complete status display of the
parameters informs on the performance
of the production line.
The flexible configuration – with
process-specific intelligence from the
Zumbach software library, provides
optimal adaptability to suit the process
and production line.
USYS 200 can be used in any
production line, e.g. in the wire and
cable industry, plastics and rubber
industry for control of tubing, pipe
hoses, etc or in the steel and metal
industry, for peeling, cold rolling,
drawing, grinding, polishing and many
other processes.
USYS 200 manages and monitors
quality and production costs by
simultaneously carrying out many
functions.
Zumbach Electronic AG
– Switzerland
Fax
: +41 032 356 0430
:
sales@zumbach.chWebsite
:
www.zumbach.chPS Costruzioni engineers
to the rescue
After a special request from Prysmian,
Aberdare, UK (formerly Pirelli),
PS Costruzioni engineers have
designed and manufactured a new
packaging line – the automatic coil
winding machine, model PS200/8-2.
This brand-new line is unique because
it can wind up short length coils
(eg 5,10,15 and 25m), with the
following dimensions:
Maximum outer diameter: 230mm;
Inner diameter: 110mm or to
be decided according to the
customer’s requirements;
Adjustable height: from 30mm-
110mm.
What is worth emphasising is the
presence in this line of a perimetral
taping unit, as well as a film drilling
one. This is designed to automatically
apply adhesive tape onto the coil outer
diameter.
The film drilling machine, located at the
exit of the tunnel, can drill both sides
of the shrink-wrapped coil, producing
a circular drilling and a hole to enable
the customer to pull the end of the
cable easily.
PS Costruzioni Meccaniche Srl
– Italy
Fax
: +39 039 689 8769
:
ps@pscostruzioni.comWebsite
:
www.pscostruzioni.com•
•
•
Research pays off
Wire cleaning is necessary to totally
remove lubricants used in wire-
drawing, in order to prepare a perfect
cleaned surface before the wire goes
for annealing in the furnace.
Fismet Industriale’s new cleaning
machine fits into the manufacturing
line and has no adverse impact on
production line efficiency. The new
machine, which is able to clean from
1 to 12 (or more) wires, is completely
automatic and works 24 hours per day.
The cleaning cycle has three phases:
washing in hot detergent solution
activated by an ultrasonic system;
rinsing in dry saturated steam and hot
air drying.
Fismet Industriale Srl – Italy
Fax
: +39 02 3350 3251
:
info@fismet.comWebsite
:
www.fismet.com