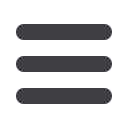

26
AFRICAN FUSION
June 2016
Out of position Stellite cladding
“
I
am going to share a
break-through applica-
tion with you today,
which involved collaboration
between the petrochemical
client, Sasol; piping contractor,
Petrochemical Piping Services;
equipment OEM, Fronius and its
local distributor BED; and Welding Al-
loys South Africa, WASA,” Zylstra begins.
As with all application related-
successes, the story startswith the client
need. “Sasol have a requirement for a
cobalt-based alloy for high-temperature
erosion resistance – and erosion in-
volves the combinationof corrosion and
abrasion, so both wear and corrosion
resistance were needed,” he explains,
adding that a cobalt-based rather
than nickel-based alloy had to be used
because of the need for hot corrosion
and sulphidation resistance from the
clad layer.
Cladding had to be applied in-
situ and out of position, while time
constraints drove the client towards
exploringhigher deposition ratewelding
processes. “Theweldingwas previously
applied using SMAW or stick electrode
welding with some manual TIG weld-
ing using consumable rods. Both these
processes have productivity issues, so
an additional requirement was speci-
fied for a procedure to be developed
that reducedwelding time,” Zylstra says.
Summarising the need, he says
that suitable cobalt consumables with
good out-of-position weldability were
required, along with a process and as-
sociated equipment to enable higher
productivity.
A history of cobalt-based alloys
After playing the Beach Boys song, Ko-
komo, Zylstra says that Elwood Haynes
developed the basic metallurgy of
cobalt-chromium (Co-Cr) alloys in the
early 1900s – in a town near Kokomo,
Indiana, USA. “And now that you have
heard that song, youwon’t forget where
Haynes came from.”
Haynes contributed significantly to
our knowledge of martensitic stainless
steels and, in 1905, he designed amotor-
car and founded theHaynes Automobile
Company.
Turning attention back to the cobalt
alloys Haynes invented, Zylstra says
that he derived the name for his alloy
from the Latin word ‘stella’, because
of its ‘star-like lustre’. Haynes formed
the Haynes Stellite Company and reg-
istered the trade name ‘Stellite’. His
company becameUnionCarbide in 1920
and Deloro Stellite in 1922. “Haynes’
cobalt-chromiumalloys for weldoverlay
cladding have been known for over 100
years and many different brand names
have emerged,” Zylstra informs us, add-
ing that the ‘Stellite’ trade name is still
owned by Deloro Stellite today.
Moving onto the history of the
Welding Alloys Group, he says that the
company was started in 1966 in Fowl-
mere, a town near Cambridge in the UK.
Originally, WAwas a hardfacing business
founded by Jan Stekly to solve abrasive
wear problems. Today, the company has
In this article, Wiehan Zylstra (right), technical manager of
Welding Alloys South Africa (WASA), presents a case study on
the use of Welding Alloys’ cobalt-based cladding material,
STELLOY 6-G, whichwas welded out of position using Fronius’
TPS synergic pulsed-GMAW equipment.
Micrographs of the STELLOY-clad layer for three different welding positions: left, from the overhead position; centre, from the 3:00 vertical up position;
and right, from the downhand position.
Cobalt-based cladding:
a local success story
10 factories producing flux-cored wires,
one of which is here in Roodepoort,
where hardfacing flux-cored wires are
produced – “98% of which are chrome-
carbide (CrC) consumables”.
As well as wire production, the busi-
ness still has production units all over
theworld. “In South Africa, for example,
52 t/a of our ownwires are used tomake
CrCoverlay plate for a range ofmaterials
handling applications for mining equip-
ment such as crushers,” Zylstra reveals.
Welding Alloys also produces a com-
prehensive range of stainless steel and
nickel-based alloys and its cobalt-based
consumable range is marketed under
the STELLOY trade name.
Metallurgy of cobalt-based alloys
The Stellite alloys are, essentially, cobalt
chromium alloys containing 50 to 60%
cobalt, hence the term ‘cobalt-based’.
Cobalt has a face-centred cubic (FCC)
crystal structure, which makes it duc-
tile like austenitic stainless steel. “But
this structure is somewhat unstable. If
exposed to mechanical stress or high
temperature, the FCC crystal structure
transforms to a hexagonal close packed
(HCP) structure, which has less ductility,
higher yield stress, a high work harden-
ing rate, good fatigue properties and
higher toughness,” Zylstra explains.
The chromium in the alloy gives it its
corrosion resistance. As with stainless
steel, the chromium forms a passivation