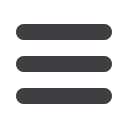

66
Wire & Cable ASIA – September/October 2017
www.read-wca.comTechnology
news
PLASMAIT GmbH from Austria is
seeing an increasing demand for its
high-output plasma heat treatment
lines for stainless steel products.
The
next
deployment
of
its
PlasmaAnnealer will take place at wire
Southeast Asia.
Plasmait sold a 30kW plasma annealer
to a renowned stainless steel wire
producer, who wants to replace its
traditional tube furnace for production of
flat ferritic and austenitic product with
widths up to 30mm.
The HPA30 plasma annealer with
output capacity of 100kg per hour will
allow the manufacturer to halve the
energy cost per kilogram of output
whilst allowing for a considerable cost
saving in terms of peak power
consumption.
Much lower power connection
requirements of the plasma annealer
also
means
cheaper
cabling
installation for connecting power.
The
new,
compact,
single-line
production will have the same output
as the old multi-line furnace and will
take about one third of the shop floor
space.
Single-line production will also reduce
material manipulation and limit the
investment into the associated
take-ups, payoffs and transport
system.
A typical plasma annealer installation
for stainless steel applications can
substitute around ten traditional lines
on a conventional strand furnace.
PlasmaAnnealer allows accurate heat
input and hence more uniform
recrystallisation, which is reflected in
homogeneous grain size in the
longitudinal and transversal direction.
The HPA30 annealer also features an
extended tempering zone to allow for
extended dwell time or slow cooling,
which is necessary for selected ferritic
grades of stainless steel.
Processed material does not touch the
plasma chamber when at high
temperature, which reduces the risk of
surface scratching. This is different to
the conventional strand furnace where
tubes remain in contact with the
furnace guiding supports during the
maximum elevated temperatures.
Plasmait GmbH – Austria
Website
:
www.plasmait.com❍
The PlasmaAnnealer HPA60 from Plasmait
Annealer for flat stainless steel wires and profiles
Wire rod rust is no longer an alarming
phenomenon, since the introduction of
the Smooth-Brush (SB) wire rod green
and dry cleaning system.
Installed in-line after a simple rod
reverse bending descaler, the SB
system removes excess rod scale and
rust, converting over 95 per cent of
rod scale into useful micro-abrading
pads, providing efficiency and
simplicity in rod dry cleaning
applications, H/C and L/C, including
0.98% C.
Continuously liberated rod scale
provides, in-line, an extremely
receptive about 5-micron size texture
enabling powder lubricant to be
chemically
and
mechanically
interlocked to the rod surface, forming
a hard and consistent anti-wear and
anti-friction conversion coating that is
found to perform comparably to or
better than zinc phosphate.
This achieves in-line direct drawing
from mechanically descaled uncoated
bare rod, at virtually zero energy
consumption and zero maintenance
cost, in a totally green and dry
application.
The SB rod cleaning is used in
demanding wire drawing applications,
including spring wire, plating wire,
galvanised wire, PC strand wire, Al
clad wire, cold-heading wire, CO
2
welding wire, etc.
The SB dry cleaning system replaces
costly operations in wire rod cleaning
processes, (including acid and other
aggressive wet chemicals), generating
substantial
cost
savings,
environmental
benefits
and
improvement of productivity.
Decalub – France
Website
:
www.decalub.comRod rust removal – dry, green and clean
❍
Rod and wire cleaning by SB brushing
system