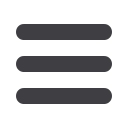

34
Wire & Cable ASIA – November/December 2014
www.read-wca.comTechnology
news
The INF-2 is a new concept pail packer, designed by Gimax,
for the process of packing wire into drums.
The INF-2 is a ‘fully packaged system’ in the sense that the
only separate entity from the main body is the driven pay-off
– both the dancer and the electrical control cabinet have
been incorporated into the main body resulting in a
reduction in space occupancy (and height), and
subsequently in costs for the end user.
The unit does not follow the traditional method of raising
and lowering the drum during the packing process. The
drum and flyer both rotate, but the INF-2 makes use of an
innovative process in which the front portion of the unit itself
slowly rises while the flyer is layering the wire within the
drum. The entire flyer assembly is of a totally new design
and concept, a different philosophy to traditional methods.
The pail packer can handle various drum types (round,
hexagonal, octagonal) and various sizes ranging from small
100kg up to the traditional 350kg drums of MIG wire, and
also up to the large 500kg drums as the unit can handle
drums with or without a central core. The unit is set up as
standard with a base that can handle both round and square
drums. Size changeover is minimal.
The unit is equipped with wire straighteners, capstan and
vibrator to settle the wire in the drum, and comes complete
with an operator platform which raises and lowers with the
machine so that all parts of the unit are easily accessible
for maintenance and for threading the wire through the
system.
The INF-2 can also be equipped with an optional video-cam
system that allows the operator to check the inside of the
drum as well as other parts of the line while the unit is in
operation.
Gimax Srl – Italy
Website
:
www.gimaxgroup.comNew concept for packing wire into drums
THE original Upcast
®
continuous
casting technology allows the casting
of copper and copper alloy rod in a
cost efficient and environmentally
friendly way. It is a simple process with
easy operation through an advanced
control system.
No harmful emissions or need for
waste treatment mean a reduced
environmental
footprint
for
GREENerCAST lines, which also have
low lifecycle costs, easy variation of
output, alternative for using scrap in
the process and unique upgradability.
As new applications for copper alloys
are being developed, the utilisation of
Upcast technology within the copper
alloys field is rapidly increasing.
Rod production lines are of a modular
design, and both single- and
double-furnace configurations are
possible. With a double-furnace
configuration – having separate
melting and casting furnaces – it is
possible to reach 40,000 tpa output,
while 12,000 tpa is possible for a
single-furnace configuration. A wide
capacity range both in single- and
double-furnace
configurations
is
available with a possibility for
upgrade.
The majority of delivered Upcast lines
are for Cu-OF rod and mainly with the
most common cast rod diameter of
8mm. Rods with bigger diameters are
used for manufacturing a variety of
products, eg bus-bars, trolley wires,
electroplating anodes, etc. Cu-OF rod
is well suited for all electrical
applications.
Upcast-Hybrid technology is based on
using the same equipment for casting
both Cu rod and tubes by modifying
certain product specific parts of the
Upcast-SGTube casting machine and
coilers to facilitate easy changeover.
The flexibility of the product mix makes
the hybrid system a truly cost-effective
solution for companies with a diverse
product portfolio.
A hybrid configuration may have two
separate furnaces from which the
casting takes place. However, at any
given time just one can be used for
casting purposes while the other would
be in a standby position allowing for
oxygen free copper melt for rod and
DHP copper for tube to be
continuously
available.
When
produced from the same type of melt,
rod and tube can be cast
simultaneously.
With this system the full capacity can
be optimised between both products
or sometimes for only the other
product.
Upcast OY and ASMAG GmbH have
found a perfect match for further
processing of Cu rod through Asmag’s
Ascon process: rotary extrusion,
drawing, finishing and packing of bars
and profiles. By combining the
respective know-how and expertise
into cast and form, the two partners
can offer proven cost saving solutions
to customers.
Upcast OY – Finland
Website
:
www.upcast.comCost efficient and environmentally friendly
❍
Use of Upcast technology is rapidly increasing