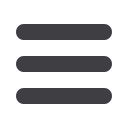

35
www.read-wca.comWire & Cable ASIA – March/April 2013
With
the
new
temperature
measurement, precision with Sikora’s
Wire-Temp 6000 reaches levels never
seen before at the heating of a
conductor
with
a
conductor
preheating.
The name says it all: The Wire-Temp
6000 continuously measures and
controls contact-free the temperature
of the conductor at the output of the
Preheater 6000 with a permanent
precise actual value of the conductor
temperature for all conductor
cross-sections, at all line speeds.
Thus, the Wire-Temp 6000 raises the
benchmark for conductor preheaters
to a completely new level. During
production there are numerous
influences on the accuracy of the
conductor temperature.
Examples
are
the
ambient
temperature, the initial temperature
of the conductor and, in particular,
the development of the temperature
of the so called ‘short-circuit wheel’
within the first 10 to 20 minutes after
starting the production or after an
interruption of the production.
The new Wire-Temp 6000 considers
these factors and determines the
conductor
temperature
indep-
endently from cross-section, material
and surface structure of the
conductor.
The Wire-Temp 6000 is optionally
integrated in the proven preheater
system Preheater 6000 and can
easily be retrofitted in existing
devices. In addition, it is available as
an independent system without the
Preheater 6000.
Sikora AG – Germany
Website
:
www.sikora.netPremiere of the Wire-Temp 6000
❍
❍
The Preheater 6000 is now available
with a temperature measurement and
control
Die drool elimination
Excess of material at the output of a die during an extrusion process, also
called die drool, can significantly reduce the production speed of a cable.
A clear comprehension of the phenomenon for any kind of polymer is not
yet available. Nevertheless there is some help to reduce the impact of
such default: PTFE-coating.
Erocarb has recently introduced a new 3-layer coating for extrusion tools
with great success. In order to save the concentricity, the mounting
surfaces remain blanked hardened steel. The only surfaces in contact with
the polymer will be coated.
As die drool appears on inside and outside surface of the extrudate,
Erocarb recommends the coating of both tip and die.
Erocarb coating is applicable on hardened steel but not on carbide.
Erocarb – Switzerland
Website
:
www.erocarb.ch