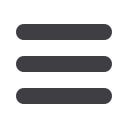

3/116
All stocked articles available within 24 hours by UPS Express.
All prices excluding VAT per piece (if not stated otherwise).
3
Clamping
Systems
Design: Protection class IP 67.
Further development of the Universal
3D probe, with improved mechanics and a new, compact housing with
good grip, for installation into milling spindles or countersunk heads.
The spindle axis is positioned accurately on the workpiece or device
edges. Any approach direction (X, Y, Z-axis). The large, analogue
1/100 mm dial gauge (2 pointers) with marked travel path (safety
distance) always deflects in the same direction and indicates the dis-
tance between the spindle axis and the workpiece edge. As soon as the
display is set to zero, the spindle axis is positioned without prolonged
attempts; without calculations, without sign problems, precisely on
the edge of the workpiece. This reduces the additional costs. increases
productivity and relieves employees. The original Haimer probe tip for
max. accuracy of 0.01 mm is changed without requiring a tool; recali-
bration of the probe is not necessary. The enlarged travel path in com-
bination with the tried and tested predetermined breaking point provide
additional safety. For maximum measuring accuracy, all 3D probes are
individually measured and aligned during installation.
Application:
For setting workpiece zero points, length and depth
measurements on milling and eroding machines (insulated probe tip)
and for centring and taking the mean of bore holes and shafts. Also
used for testing the straightness and evenness of surfaces.
Supplied:
3D probe with short probe tip ∅ 4 mm.
Order
No.
Shaft ∅
mm
3777
Ball tip ∅
mm
Display accuracy
mm
Housing ∅
mm
Length without clamping shaft
mm
0010
12
276.00
4
0.01
62
100
(392)
B
D
H
L
3D probe NEW GENERATION, IP 67
Design: Protection class IP 67.
The smallest 3D probe in the world,
for installation into the milling spindle or the countersunk head; the
spindle axis is positioned precisely on the workpiece or device edges.
Any approach direction (X, Y, Z-axis). The size of the Zero Master is
adapted to small machines. The small, analogue dial gauge always
deflects in the same direction and indicates the distance between the
spindle axis and the workpiece edge. As soon as the display is set
to zero, the spindle axis is positioned without prolonged attempts;
without calculations, without sign problems, precisely on the edge of
the workpiece. This reduces the additional costs. increases productivity
and relieves employees. The clamping shaft has a diameter of 10 mm
and can therefore also be used on machines with SK 30 or with small
HSK spindles. Large workpieces can also be measured through the
shortened housing, which projects only a little way out of the spindle.
The probe tip is changed without requiring a tool; recalibration of the
probe is not necessary. The enlarged travel path in combination with
the tried and tested predetermined breaking point provide additional
safety. For maximum measuring accuracy, all 3D probes are individually
measured and aligned during installation. The Zero Master can be
equipped with a short (ball ∅ 4 mm) and a long (ball ∅ 8 mm) probe
tip. The probe tips are compatible with all other Haimer 3D probes.
Application:
For setting workpiece zero points and length
measurements on milling and eroding machines (insulated probe tip)
and for centring and taking the mean of bore holes and shafts.
Supplied:
3D probe with short probe tip ∅ 4 mm.
Order
No.
Shaft ∅
mm
3777
Ball tip ∅
mm
Display accuracy
mm
Housing ∅
mm
Length without clamping shaft
mm
0000
10
276.00
4
0.01
49
96
(392)
Zero Master analogue, IP 67
IP 67
IP 67
3D probe
656