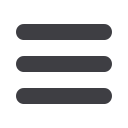

F
ittings,
C
ouplings &
T
ubular
J
oints
J
anuary
2008
www.read-tpt.com124
›
Tubular components can offer significant
improvements with respect to performance,
weight, and cost. Joining technologies like
gas metal arc welding (ie MIG welding),
gas tungsten arc welding (ie TIG welding),
and laser welding, create challenges
when welding large volumes of tubular
components.
Issues include burn-through and the need
to move the welding heat source and/or
filler metal source around the weld joint in
tight spaces. These processes create even
greater challenges when joining dissimilar
materials and in the welding of tubular
components made of coated materials (eg
galvanized steel).
Edison Welding Insititue (EWI) is involved
in the development of two new technologies
designed for joining of tubular structures:
deformation resistance welding (DRW) and
magnetic pulse (MP) joining technology.
DRW is a resistance welding process which
uses conventional resistance welding
machines and forms near instantaneous,
leak-tight welds. DRW was initially
developed for tube-to-tube joints but this
technology extends to tube-to-heavy-
section components such as heavy-wall
pipes, fittings, and other solid and hollow
parts or components. Other applications
for DRW technology include hydraulic lines,
exhaust systems, and suspension/frame
components.
MP joining configures two tubular parts
to form a lap-type joint, and provides
the opportunity to achieve welding or
mechanical joints as required by the
application. The weld generated by this
technology is characterized as a solid-state
weld.
The basic requirement of the process is
that the outer tube is electrically conductive
and possesses contain amounts of plastic
deformation capability. The inner tube
can be a different material that is either
conductive or non-conductive.
The passage of a high current discharge
through the specially designed coil (or coil
bank) creates an induction current (eddy
current) in the conductive outer tube. The
interactions of the two magnetic fields
generated by the primary discharge current
and the eddy current result in the repulsion
force between the coil and the outer tube.
This powerful repulsion force causes the
outer tube to impact on the inner tube at a
velocity that is sufficiently high to generate
bonding in a matter of microseconds.
MP joining development work at EWI
includes the welding of dissimilar materials
for various industries such as automotive,
heavy manufacturing, and aerospace.
Applications that include welding aluminium
alloys to steel are common for MP
technology.
Other applications of applying thin-gauge
material to large tubular components
as a dissimilar coating are also being
investigated. The MP joining technology
and DRW processes will enable product
designers to extensively use tubular
sections in various components for cost,
performance improvement, and weight
reduction.
This article was supplied by Menachem Kimchi,
Business Development Engineer, EWI (Edison
Welding Insititute).
Edison Welding Institute
– USA
Fax
: +1 614 688 5001
:
menachem_kimchi@ewi.orgWebsite
:
www.ewi.orgTube and fitting system for
thermal installations
Eurotubi Pressfitting, from Eurotubi Europa,
Italy, is a system of tubes and fittings used
for hydrothermosanitary installations, and is
suitable for the conveyance of water, gas,
and compressed air.
The fittings at the extremities of the O-ring
seating are able to support high pressures
and temperatures over 85°C. Tubes
and fittings are assembled through the
permanent deformation of the fitting by
special pressing jaws mounted on small
electromechanical tools. Once pressed, the
o-ring ensures hermetical connection.
The Pressfitting system combines the
reliability of joints with a quick and easy
method of laying, as it requires no gluing,
threading or welding. A wide range of
fittings are available in diameters from
15mm to 108mm in stainless steel 316L,
and in diameters from 12mm to 108mm in
carbon steel.
The quality of materials, constant sealing
and duration tests, and rigorous quality
control allow the Eurotubi Pressfitting
System to obtain conformity within strict
European certifications. Carbon steel
provides a competitive and innovative
solution for thermal installations, offering
the same quality provided by traditional
copper systems, but at a lower cost.
The Eurotubi Pressfitting System is also
compatible with most significant brands of
fittings.
Eurotubi Europa
– Italy
Fax
: +39 0362 41099
:
info@eurotubieuropa.itWebsite
:
www.eurotubieuropa.itAdvances in welding tubular components
fi
Figure 1 (below left and right): deformation resistance welding (DRW) tube to a solid part; and bottom (left
and right) magnetic pulse weld – aluminium to steel