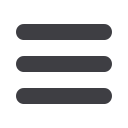

C
oating,
J
acketing & Galvanizing Technology
J
anuary
2008
www.read-tpt.com84
›
Until now only batch galvanized material
was available for piping in application areas
where there is a high risk of corrosion, eg
‘dry’ sprinkler systems. Weak points in the
zinc coating often reduce the service life of
the piping. However, welded pipes made
of continuously galvanized steel, where
the welds are galvanized on the inside and
outside, offer a higher level of protection
against corrosion.
As Mr Harald Leitner (BEng), sales manager
of WProfile & WPipe at Wuppermann
Stahl GmbH, Austria, states,
“The level of
corrosion protection offered by pipes that
are manufactured using our process is far
superior to the protection offered by batch
galvanized pipes.”
Due to their increased resistance against
corrosion, galvanized tubes are used in
numerous application areas, including
manufacture of water and sprinkler pipes,
scaffolding, racking systems, fencing and
playground equipment. The pipes are
made of ‘black’ (ie non-galvanized steel
strip), which is rolled to form a tube and
then longitudinally welded. The zinc layer
is subsequently deposited by way of batch
galvanizing, ie by dipping the tube in a bath
of molten zinc.
This conventional dipping process does,
however, have one major disadvantage.
An intermediate layer is formed as a result
of the tube being dipped in the molten zinc
for a long period of time. The metallurgical
reaction of the iron with the zinc leads
to the formation of intermetallic phases.
The thickness of this layer increases
proportionately to the temperature and
the dipping period. In the case of batch
galvanizing, the percentage in the overall
thickness of this layer can often be as high
as 70-80 per cent, while the actual zinc
layer only accounts for 20-30 per cent.
As comments Mr Markus Dirschlmayr
BEng, marketing department:
“This layer
of intermetallic phases has negative
properties”.
The corrosion protection effect
of a zinc coating is based on the fact that
this metal corrodes very slowly.
In areas where the underlying steel has
been exposed, eg as a result of a scratch,
the zinc acts as a
‘sacrificial anode’
which
continues to protect the exposed steel.
However, when the upper layer of metallic
zinc is used up and the corrosion attacks
the underlying intermetallic phases, the iron
atoms react with the oxygen.
This problem is further magnified by the
fact that the intermetallic layers are brittle.
The danger of flaking in the presence of
mechanical stress, eg during the forming
process, increases proportionately to the
thickness of this layer. Corrosion protection
is greatly reduced in such areas.
However, the disruptive intermediate layer
is reduced to a minimum during continuous
galvanizing. As states Mr Harald Leitner,
“In
contrast to the conventional procedure, our
Wgalweld process uses strip stock galvanized
in a continuous process prior to welding”
.
Contact with the zinc bath only lasts for a
fraction of a second and, as a result, the
intermetallic phase is extremely thin and
therefore does not have a negative impact
on the durability of the layer or corrosion
resistance.
The share of metallic zinc in the coating is
over 99.9 per cent. Moreover, this process
is very easy to control due to the utilisation
of modern process control technology. The
thickness of the layer can be set with tight
tolerances. Furthermore, zinc coatings of
different thicknesses can be deposited on
the upper and lower surfaces.
Steel strip galvanizing technique leads to
next generation galvanized pipes
fi
(Below left) protective coating – in batch galvanizing, the steel components are dipped into a huge bath full of molten zinc (photo: Klaus Vollrath ); and (below right) tube
production – the steel strip, which is formed into a tube in a rolling process, is then longitudinally welded. Immediately afterwards, the inner and outer sides of the weld
are continuously galvanized (photo: Klaus Vollrath)
›
Boundary layer – the metallurgical reaction of
the iron with the zinc leads to the formation of
intermetallic phases which, in the case of batch
galvanizing, often makes up for 70-80 per cent
(photo: Wuppermann Stahl)
88