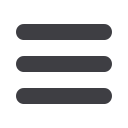

C
oating,
J
acketing & Galvanizing Technology
J
anuary
2008
www.read-tpt.com86
›
During the tube manufacturing process,
the steel strip is rolled using state-of-
the-art equipment to form a tube and
inductive longitudinal welding is then
carried out. Immediately afterwards, the
inner and outer sides of the weld are
continuously galvanized using a process
that is patented by the US company
IDOD.
The result is a fully protected tube that is
fully protected against corrosion. Once
the zinc layer has been deposited, the
continuous tubing is cut to the required
length in an automatic cutting station.
This process consequently leads to
improved corrosion protection. Says Mr
Ralf Komor BEng, regional manager
(central Europe) at Victaulic in Nazareth
(Belgium),
“As the zinc coating contains
hardly any intermetallic phases compared
to conventional batch galvanizing and is
made up almost completely of metallic zinc,
the corrosion protection effect lasts a lot
longer.”
Another essential factor is the improved
adhesion of the zinc coating when subjected
to mechanical strain. This is particularly
significant from a cost perspective as time-
saving processes such as
the fast coupling system
from Victaulic are preferred
when installing pipes.
Here, the ends of the pipes
are connected using a
special coupling that sits
exactly in the groove. The
grooves are rolled into
both pipes using a special
device.
This rolled groove is a
potential weak point when
using conventional batch
galvanized piping as the
intermetallic phases could
flake off under mechanical stress, thus
reducing the corrosion protection.
The process also leads to even greater
flexibility. It applies not only to the pipe
diameter and the wall thickness but also
to the thickness of the zinc coating and the
steel alloy that is used. The pipe lengths are
a very important aspect: due to the state-of-
the-art cutting station, the pipes are cut to
millimetre precision. This saves money as
each adjustment on the construction site is
an important cost driver.
If required, these pipes can also be
supplied with the groove already rolled.
While batch galvanized piping material can
normally only be supplied in 6m lengths,
the Wgalweld pipes are available in any
required length from 2.5m to 14m. This
paves the way for significant savings in
the areas of materials and working hours
as fewer connections are required over the
total length of the pipes.
The superior zinc coating of the Wgalweld
pipes is particularly suitable for dry
sprinkler systems as the constant change
between wet and dry phases inevitably
results in greater exposure to corrosion.
Other interesting application areas, apart
from the construction industry and chemical
plant construction, include the automotive
industry and all other areas that have high
corrosion resistance requirements.
This article was supplied by Mr Klaus Vollrath
(kvollrath@bluewin.ch), Schnitt-Stelle Redaktionsbüro,
Switzerland.
Wuppermann Stahl GmbH
– Austria
Fax
: +43 50 910 285
Website
:
www.wuppermann.comVictaulic Europe BV
– Belgium
Fax
: +32 9 3804438
Website
:
www.victaulic.beHardening and tempering of oil country components
Can-Eng Furnaces is a North American designer and manufacturer of industrial heat
treating equipment. The company is due to supply a 30" x 36" 48" integral quench (IQ)
furnace with companion charge car, post wash, two tempers, and Endo gas generator to
the Serov Mechanical Plant (SMZ) in Serov, Russia.
Load capacity of the system will be 5,000lb gross. The equipment will be containerised
in the company’s Niagara Falls facility for overseas shipment to the Ural Mountain
region. Once operational, in the first quarter of 2008, the line will be used for the
hardening and tempering of oil country components.
Line automation will include a Siemens S7 PLC, and the unit will incorporate the latest
in fuel saving indirect fired burner technology, long life radiant tubes, and high velocity
uniform oil quenching.
Can-Eng’s product lines include continuous mesh belt furnace systems, batch integral
quench furnace systems, continuous steel bar heat treatment systems, nonferrous T4,
T5, T6, T7 heat treatment systems, basketless heat treatment systems, and modular
aluminium heat treating systems.
Other systems include precision air quench systems, primary aluminium processing
furnace systems, a Scada system, process enhancement technology, and a wide array
of custom furnaces solutions. The company also offers a comprehensive after-market
support team, delivering system upgrades, technical support and spare parts.
Can-Eng Furnaces
– Canada/USA
Fax
: +1 905 356 1817
:
furnaces@can-eng.com•
Website
:
www.can-eng.comfi
Strong bond – the zinc coating on WGalweld tubes also remains intact
in spite of the mechanical strain the pipe is exposed to when rolling the
groove (photo: Klaus Vollrath)
›
Weak point – the likelihood of the intermetallic
phase layer flaking off when subjected to
mechanical stress increases proportionately to
the thickness of the layer. Corrosion protection
no longer exists in exposed areas (photo:
Wuppermann)
88