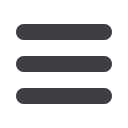

CAPITAL EQUIPMENT NEWS
JANUARY 2016
5
individual options for every individual cus-
tomer – from single machines to integrated
solutions for the entire process cycle.
THE GLOBAL NUMBER ONE
When it comes to roads, the Wirtgen Group
offers impressive, innovative solutions,
internationally recognized processes and
a mature, seamless range of products that
satisfies the most exacting demands. Be it
for earthwork and rock construction, new
road construction or road rehabilitation,
asphalt or concrete roads, narrow cycle
tracks or airport runways around the world
– the Wirtgen Group offers its customers an
impressive range of products and services.
MANY STEPS PAVE THE WAY
The first person in the paving team, however,
is the truck driver who fills the asphalt
into the paver’s hopper. Two mutually
independent conveyors transport the
material through the machine to the rear,
where it is uniformly distributed between
paver and screed by two individually
controlled rotating screw conveyors. When
paving a standard mix, the temperature
should always remain above 110 °C in order
to ensure sufficient time for compaction.
The hot mix should be covered when deliv-
ered by charging trucks to ensure that the
paving operation is carried out in the most
suitable time frame. To guarantee continuous
paving, the capacity of the asphalt mixing
plant always needs to be higher than the pav-
er’s laydown capacity. If the paver stops mov-
ing due to lack of material, disruptive lateral
joints occur as a result of the paved layer
cooling down. When paving standard mix,
the paving temperature should be higher
than 110°C to allow an as large time frame
as possible for compaction.
PAVING WITH THE ROAD PAVER
All paving units need to be heated prior
to commencing the paving operation to
prevent the mix from sticking to sensitive
parts of the machine. On modern pavers,
the compacting systems in the screed can
be actuated separately. Particularly the
high compaction screeds achieve very good
compaction. As a result, the rollers behind
the paver require fewer passes to achieve
the specified final degree of compaction.
Compaction effected by the high-density
screed enables the rollers which follow be-
hind the paver to achieve the overall final
density specified by the client in fewer roll-
er passes. In most cases, the road paver is
geared for either high density or fast ad-
vanced speed, both of which have an effect
on the number of roller passes required.
GETTING THE ROLLERS READY
Rollers are heavy road construction
machines used for compacting hot and
therefore flexible asphalt pavements. To
prevent them from causing damage to the
new asphalt surface, they must not come
to a stop during the compacting operation.
For precisely that reason, machine
maintenance is of particular importance. In
addition to that, checks need to be carried
out prior to commencing work to make sure
that the drum is clean, that fuel and engine
oil are available in sufficient quantities, and
that the water tank has sufficient water for
the drum spray system.
Basically, compaction becomes more ef-
fective with increasing temperature of
the paved mix. The most advantageous
temperature range depends on the com-
position of the mix, the thickness of the
pavement and the type of binder used.
The roller operator starts compaction at the
COVER STORY