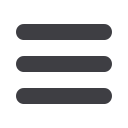

T
ube
M
ills
and
R
oll
F
orming
L
ines
www.read-tpt.comN
ovember
2009
115
›
LINSINGER Austria produces milling
machines for pipe mills.
For plate edge processing, the company
uses the principle of circumferential
milling.
Pipe manufacturers continuously check
their plants for productivity and operating
costs.
In the field of weld seam preparation,
pipe mills cannot avoid milling technology.
Previously used processes such as trimming
the edges with rotary shears demonstrate
serious disadvantages.
Flaws and structural deformation of
welding edges produce seam defects, and
high material costs are caused by process-
related oversizes.
A well-known Asian pipe mill, which
already has over 15 Linsinger machines
in use, focuses on the approved strip
edge milling of Linsinger. After one year
of production, management observed that
productivity had increased and operating
costs had decreased, while pipe errors were
reduced to almost nil.
AdvantagesofLinsingerstripedgemilling
machines include a flawless and clean
metal surface, no structural deformation
through cutting processing because the
surface does not warmup, and interference-
free chip flow on account of short chips,
which are disposed of by chain conveyor
belts.
Height copying milling units ensure
precise welding edges, including corrugated
plates, and perfect exploitation of carbide
plates. Accurate welding slit is caused by
Viable alternatives to using rotary shears
Linsinger’s BFMK 90/800D double strip edge milling machine
higher precision of produced welding edges,
and a 45m/min welding speed is possible.
Linsinger Maschinenbau GmbH
– Austria
Fax: +43 7613 8840 38
Email:
maschinenbau@linsinger.comWebsite:
www.linsinger.comUNIVERSAL Tube & Rollform says it is
a one-stop equipment source for tube
machinery and coil processing.
Its 125,000 square foot warehouse is fully
stocked and ready for a hands-on inspection
Complete tube and rollform needs catered for
of equipment. Universal Tube & Rollform,
part of the Universal Controls group, says
it aims to serve the growing needs of the
tube, pipe and rollform industry and offers a
variety of cost efficient services.
From concept to production, it claims it
canhelpcustomersreachtheirmanufacturing
goal. Fax or email a drawing of the shape
you need to fabricate, and its experienced
team will get to work assembling a
complete line quotation to produce the part
that is required.
The company also claims it will save time
and money by using quality reconditioned
machinery, combined with new expandable
mill control systems and components at
today’s highest standards.
Customers can inspect the line running in
the shop itself, while it making the part, prior
to delivery.
Universal Tube & Rollform can also help
with start-up and training at the customer's
own site.
Universal Tube & Rollform
– USA
Fax: +1 419 874 2825
Email:
sales@utubeonline.comWebsite:
www.utubeonline.com
An example of Univeral Tube & Rollform’s stock, housed in its 125,000 square foot warehouse