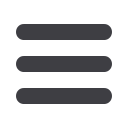

Industry News
www.read-tpt.com8
J
uly
2015
Kusakabe supplies
two pipe mills
KUSAKABE Electric & Machinery
has supplied and commissioned two
pipe mills in Taiwan for CHS Steel in
conjunction with several other suppliers.
This new installation is for a state-of-the-
art operation and will make it the most
advanced in Taiwan.
The 4" tubing line manufactures tubes
from 60.3 to 114.3mm up to 10.5mm
thick, and steel grades with tensile yield
strengths up to 750MPa. The line starts
with the uncoiler and shear welder,
vertical looper (strip accumulator) all the
way through to the hydrostatic pressure
testing, UTS, coating and packing in a
continuous process.
The tubing line itself incorporates
Kusakabe’s vertical looper (strip
accumulator), flying strip shear and sub-
based stands with independent drive to
each shaft for quick changeover and
improved drive.
One squeeze stand is provided in a
four-roll configuration, with internal and
external weld bead removal and swarf
chopping.
After the weld seam annealing and
cooling stage a rotary sizing mill sizes
the tube to the customer’s requirements
before it is cut to length by a three-
bladed rotary cut off.
The 13" casing line manufactures
tubes from114.3 to 355.6mmup to 16mm
thick, and steel grades with tensile yield
strengths up to 750MPa. The line starts
with the uncoiler and shear welder,
horizontal strip accumulator all the way
through to the hydrostatic pressure
testing, UTS, coating and packing in a
continuous process.
The pipe mill itself incorporates
Kusakabe’s latest universal forming,
followed by three cassette fin passes
and a five-roll squeeze stand, and
internal and external weld bead
removal and swarf chopping. After
the weld seam annealing and cooling
stage, a rotary sizing mill sizes the tube
to the customer’s requirements before
it is cut to length by a two-bladed milling
cut off.
The strip accumulators provide CHS
with continuous operation while the
flying strip shear reduces changeover
times and strip wastage when roll
changes are required.
The configuration of the forming
sections allows for rapid change over
and easy adjustments while individual
drive motors on each shaft provide
equal distribution of the driving force
through all the forming rolls.
The squeeze stands provide for the
ideal strip presentation for HF welding
with maximum rigidity, which provides a
stable welding environment.
The rotary sizing mills are a patented
process for sizing tube and pipe. The
RSM has several advantages over
traditional sizing methods.
The outside diameter (OD) variation
is considerably less; weld seam
location can be accurately controlled;
the average OD can be adjusted very
accurately by a single point adjustment;
the tooling can infinitely cover a range
of diameters typically around 15mm;
tooling wear is reduced and does not
affect the performance of the process;
and there are no tooling marks on the
pipe and the surface finish is improved.
Tooling changes are also simple and
fast.
The two-bladed rotary cut off is a
chipless process, which is fast and the
operating costs low. In this application
the OD surface is chamfered and the
ID weld bead swarf is cut at the same
time.
The two-bladed milling cut off on
the casing line provides a square cut
end, which minimises any additional
machining operations that may be
required. The pipe is cut with tungsten
carbide-tipped saw blades.
Kusakabe Electric & Machinery Co,
Ltd
– Japan
Email:
sales@kusakabe.comWebsite:
www.kusakabe.comFeaturing:
• CNC Pipe Benders up to 10”
• BendPro CNC
• Overhead Clamp
• In-House Tooling
• Made in the
U
S
A
12” 3D!
Benders
•
Tooling
•
Parts
•
Service
| tel 253/922-7433 | fax 253/922-2536 |
8” 20D!
Powerful
Pipe Benders
www.JesseEngineering.com“Click on Pipe Benders”