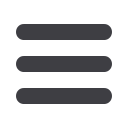

Industry News
www.read-tpt.comJ
uly
2015
15
Polysoude opens its doors in Nantes
POLYSOUDE held open days at its
Nantes, France, headquarters in
June. Over the two days, the company
presented its latest developments in
the fields of welding and weld overlay
cladding using the TIG and TIGer
(GTAW) process. Professionals and
decision-makers from all industries who
use welding in their line of business
were invited to come and discover how
they can optimise their productivity
and guarantee a quality product.
Representatives of the specialised trade
press were also welcome.
Polysoude has always aimed to
optimise its customers’ productivity while
improving the quality of their products
by developing new solutions that tackle
the most complex issues. Workshops on
different topics, described below, offered
opportunities to exchange information
on the various types of mechanised and
orbital TIG/TIGer welding and cladding
applications. These applications are
commonly used across a wide range
of sectors such as conventional and
nuclear power plants, solar farms, oil
exploration, aerospace, processing of
foods and pharmaceutical products,
water treatment, etc.
For orbital welding, it can be easily
demonstrated that using the hot-wire TIG
process with an open head significantly
increases welding speed and can be
used to join thicker tubes than the cold-
wire TIG process. Automation via a
program recorded in the power source
guarantees flawless production.
For very thick-walled parts, another
way of increasing productivity in addition
to the hot-wire TIG process consists of
reducing the groove, and therefore the
volume to be filled by the weld. The use
of an open-type carriage welding head
equipped with a narrow gap torch limits
the quantity of metal to be deposited.
Additional gains are made on preparing
the groove by limiting the loss of material
and the machining time. This technology
guarantees a quality weld thanks to the
TIG process and is perfectly reproducible
by virtue of automation.
When high quality welds are
required, orbital TIG welding is the ideal
technology for tube-to-tube or tube-to-
tubesheet welding applications. With
or without filler wire, this is a stable,
reliable process that can be used on
steel, stainless steel, titanium and nickel
and aluminium alloys, for example. The
development of a welding programme
guarantees a high-quality weld through
automation. The welding cycle can be
repeated as often as necessary with the
same result.
Orbital welding equipment can be
used in difficult conditions such as a
confined space or where there is a lack
of accessibility or visibility. On all of these
machines, the welding parameters can
be checked and compiled into a printable
protocol for guaranteed traceability.
Another application of the TIG process
is TIGer cladding. To increase their
lifetime, components are coated in
a resistant layer by the weld overlay
cladding technique.
Polysoude
– France
Website:
www.polysoude.com www.mac-ndt.com/intrasPut Us To The Test
In 1975, MAC led the way
in flux leakage testing
Forty years ago, MAC
engineers introduced
Rotoflux®, a new test system
that could detect
ID/OD defects in heavy-wall
magnetic tubular products.
Today, MAC’s high-speed
flux leakage systems are
the benchmarks for OCTG
testing throughout
the world.
TPT-JULY 2015 HALF.indd 1
5/20/15 1:52 PM