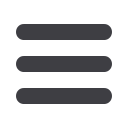

Technology News
www.read-tpt.comJ
uly
2015
45
Pipe robots for the internal
grinding of welding seams
MACHININGof weld seams is necessary
whenever the quality assurance and
safety of the seams are subjected to
high stresses.
Specialised in the development and
production of self-propelled, tethered
pipe robots for the interior inspection
and non-destructive testing of complex
pipeline systems, Inspector Systems
also offers technologies for interior
machining. The basic structure of all of
the robots consists of several drive units
with special rubber coated wheels that
are flexible and connected to each other
and to the testing or machining module
by means of folding bellows. This
modular design ensures a high degree
of bendability and allows insertion into
the pipe system, even when only a small
amount of space is available – such as
with open armatures or flanges.
Due to the pneumatic pressing of
the rubber wheels against the inner
wall of the pipe, the robot gets centred/
stabilised and is able to drive through
bends ≥1.5D as well as horizontal and
vertical sections, in particular of so-
called ‘non-piggable’ pipeline systems.
With its grinding robot technology,
approved by renowned international
companies and expert organisations in
the offshore, oil and gas and nuclear
industry, Inspector Systems has the
technical know-how to competently
grind welding seam connections from
the inside and thereby prolong their
fatigue.
Beside the removal of weld undercuts
the qualified two-step process (grinding/
polishing) eliminates surface cracks as
well as corrosion areas or any other
kind of debris and defects. Additionally,
a prevention of surface cracking is given
and even a difficult conditioning of the
misalignment between pipe ends can be
performed. Once the robot has reached
the location inside the pipe, the grinding
module is fixed by a clamping system.
Controlled by an on-board grinding
camera, a powerful three-phase current
motor with changeable grinding disc
mounted on a rotating unit (380°) and
a radial stroke makes it possible to
machine local areas point by point with
an accuracy of 0.1mm.
Standard robots from inner diameter
75mm to 1,200mm are available for
visual inspections combined with
possible laser measurements for
online defect sizing and evaluation of
the interior pipe ovality or weld seam
profiling. A 100 per cent determination of
the wall thickness or detection of pitted
areas can be done by using available
ultrasonic robots. Customised robots
can also be produced.
Inspector Systems
– Germany
Website:
www.inspector-systems.com