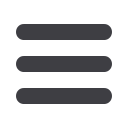

J
uly
2015
89
SMS Elotherm GmbH
Article
SMS Elotherm GmbH
– Germany
Website:
www.sms-elotherm.comIt is for these reasons that, for example, the safety-critical
fastener elements in offshore platforms for the production
of oil and gas are heat-treated with the described induction
technology.
Heat treatment without surface
decarburisation
Due to the long residence time of the heated material at high
temperatures, especially in the austenitic area, an undesired
surface decarburisation of the heated material normally takes
place in conventional combustion furnaces.
This negative effect weakens the workpiece in the area close
to the surface and leads to an inhomogeneous hardness
over the whole cross section of the material. No such
decarburisation takes place in induction quench and temper,
as the material is kept at a high temperature for a very short
period of time only.
The microstructure produced by the induction heat treatment
does not contribute to a further decarburisation of the surface,
but, on the contrary, even reduces the ferrite pockets.
The extremely short preheating and residence time at
The result of the induction Q & T process of tubes: convincing
straightness
Typical homogeneous temperature between head and tail of long
products moving through an Elotherm TemperLine™
Easy change-over of the induction coils to a different diameter
austenitisation temperature also minimises the formation of
scale during heating. In this way, not only the material yield
is all in all higher, but especially the service life of the roller
tables is significantly extended.
In conventional heat treatment lines, these conveyor units are
heavily stressed by the strongly abrasive effect of the brittle-
hard scale and they wear rapidly, with the rollers having to be
re-machined or replaced frequently.
Innovative solutions for
new products
The exploration of some oil or gas fields requires casing tubes
for lining the actual drill hole that must withstand extreme
loads. For example, in many particularly deep drill holes, low
ambient temperatures or salt water require the use of casing
tubes that must satisfy very stringent requirements in terms of
strength or leak proofness. These casing tubes typically have
an outside diameter from 5 to 10¾" with upset-end diameters
of up to 16".
The special challenge in the induction process lies in the
substantial difference in weight between the straight tube
body and the upset ends, which according to the relevant
specification API 5CT may amount to 65 per cent.
To be able to still have a uniform austenitisation temperature
and homogeneous hardness and microstructural conditions
after tempering, additional heating of the upset ends is
needed. For this, induction preheating coils are arranged
upstream of the actual austenitisation system.