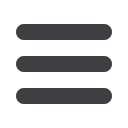

OCTG
water, gas &
44
Tube Products International April 2008
www.read-tpi.comPE 100 and cast iron pipe fittings
Dokerler Dokum Plastic Polyethylene Industry And Trade Inc, Turkey, is a major manufacturer of
PE 100 and cast iron pipe fittings for city water and gas systems. The company is researching
several solutions in city water and gas applications by transferring its wide experience and high
quality in asbestos cement, PVC and GRP, and cast iron fittings to PE 100 fittings.
PE 100 fittings bearing the Dokerler brand name are manufactured according to the requirements
of the high technology, and meet the standards such as TSE (TS 418-3 EN 12201-3 and TS EN
1555-3) and ISO 9001:2000. The fittings are produced as Electrofusion (EF) and Spigot for both
PN 10 and PN 16 operating pressures.
All Dokerler EF fittings come with an adhesive label with a standard barcode for use with
electrofusion welding machines. All the necessary information for the welding process is
entered into the welding machine automatically with the help of this barcode, in order to
minimise operator errors.
Dokerler Dokum Plastic Polyethylene Industry And Trade Inc
– Turkey
dokerler@yahoo.com•
www.dokerler.comA Dokerler coupler,
▲
▲
showing the barcode
for use with electro-
fusion welding machines
Borusan Mannesmann Boru operates
five mills – four in Turkey and one in
Italy – with a total production capacity
of 925,000 tons, and is one of the five
largest steel welded pipe producers in
Europe.
At its Izmit plant, which has a current
total capacity of 200,000 tons, the
company produces SAW (submerged
arc welding) spiral line pipes between
14" and 100" in diameter, for oil, gas and
water pipelines, and piling applications.
The company has wide experience and
a long track record in oil and gas
pipeline applications, both in Turkey and
international markets, with high grade
API standards.
Borusan Mannesmann Boru operates
under the ‘Six Sigma’ methodology,
segmenting its activities according to
customer needs. The Projects segment
specialises in pipeline solutions/
contracts, providing SSAW large
diameter and ERW pipe solutions,
and offers customers specific project
contract solutions.
Spirally welded pipes have been used all
over the world for high-pressure pipeline
projects, due to their high quality and
suitability as high strength steel pipes.
In addition to being an alternative to
longitudinally welded pipe, spirally
welded pipe has other advantages. No
calibration process (cold expanding or
roll sizing) is necessary. The diameter
tolerance of the pipe end and body of a
joint is small, particularly with regard to
ovality. The mechanical properties are
present in the base material. Since any
cold expansion reduces the material’s
ductility, the spiral-weld pipe has a higher
safety margin. When carrying out field
cold-bending, it is not necessary to take
the weld seam position into account.
There is a favourable orientation of the
weld seam and of the strip’s direction
of rolling relative to the direction of
principal stress.
The submerged arc welding (SAW)
process is widely used for welding thick
sections, but can also be applied to
plate as thin as 4mm. The principle
of spiral pipe production is to bend
steel strip spirally into a cylindrical pipe
shape, and weld the edges together.
The high currents obtained by multiple
electrodes generate considerable heat,
which leads to deep penetration of the
base metal.
Borusan Mannesmann Boru exercises
control of the contour of the deposit
and the extent of the penetration into
the base metal. These two factors have
an important effect on the chemical
composition andmetallurgical properties
of the weld metal.
The company’s standards for high
pressure gas/petroleum line pipes
include: optimum weld geometry within
narrow tolerances; hardness in weld and
HAZ max 248 HV5; OD tolerance of pipe
body equal to OD tolerance of pipe end;
no repeated weld repair; no pipe with
skelp-end weld; 100% U/T, 100% x-ray
and 100% visual inspection; process
control by metallographic examination;
and retention of quality records for a five
year period.
The company offers a wide range of
anti-corrosive coatings, including
cement mortar, epoxy and polyurethane,
polypropylene and polyethylene, and
bitumen and coal-tar enamel. For
three-layer polyethylene coating, the
pipe surface is first cleaned by shot
blasting, then preheated to the required
temperature using an induction heating
system. Following preheating, epoxy
primer is applied to the pipe surface, and
the extruded adhesive and polyethylene
are coated to the pipe by the wrapping
method. Finally, the pipe is cooled with
water.
Polyethylene coated steel line pipe
incorporates the good properties of steel
andpolyethylene. BorusanMannesmann
Boru’s three-layer PE coating has the
following advantages: wide service
temperature range; superior adhesion
strength; high resistance against
mechanical damage during shipment,
storage and laying; high, long-lasting
electrical coating resistance; resistance
against thermal and light ageing; and
perfect bendability on-site by using
adequate tools and in accordance with
the relevant standards.
The benefits of spiral welding