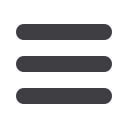

September 2016 TUBE PRODUCTS INTERNATIONAL
53
Marcegaglia
– Italy
info@marcegaglia.com www.marcegaglia.comToday, Marcegaglia, at its plant in Ravenna, Italy, the main
manufacturing unit dedicated to flat carbon steel and the
intermodal logistic hub of all group’s activities, is aiming at
increasing the production of hot-dip galvanised dual-phase
DP600 steels, manufactured in accordance with EN 10346,
and, with its internal R&D team, on the higher grades DP800
and CP800.
These steels allow vehicle weight reduction, actively
contributing to carbon dioxide emission reduction (as regulated
by the EU), while guaranteeing maximum safety. The hot-dip
galvanising process also allows higher durability in terms of
corrosion resistance and better performance in the long-term.
Magnetic steels: new semi-processed
grade M310-50K
Today, the R&D in the magnetic steels field is focusing – both
for GO (grain-oriented) and NGO (non-grain-oriented), which
represents about 80 per cent of the market – on improving the
efficiency of electrical motors by selecting materials with high
magnetic properties.
This is a result that can be attained only through the
optimisation of the entire manufacturing process: from hot
rolling to cold rolling and skin-passing steps.
Accordingly, Marcegaglia presented, during the “7
th
International Conference Magnetism andMetallurgy WMM ’16”
the development of the new grade of semi-processed
magnetic steel M310-50K, based on a 2.0 wt% Si non-
oriented magnetic steel through the optimisation of the
microstructural characteristics of the semi-finished product by
means of the thermo-mechanical processing (TMP) conditions
and the following cold rolling, annealing cycle and skin-pass
processes.
Microstructure and ODF analyses were carried out on samples
that were hot rolled, cold rolled and annealed, and after final
decarburisation and secondary recrystallisation annealing.
The results of the case study confirmed that in order
to develop favourable textures and to achieve the target
magnetic properties a thorough approach for the whole
production chain has to be adopted.
Pre-painted steels: two new finishes
for unique aesthetic levels with
steel safety
In the pre-painted steels sector, Marcegaglia is developing
new finishes with high aesthetic qualities giving efficiency and
durability, along with the safety of the steel itself. This is the
case, for example, with the brand-new product that simulates
wood surfaces – in three colours and finishes – through a
process of painting and finishing directly on steel.
It is an innovative coating that can be used for several
applications, especially in the field of architecture, that
combines the aesthetic value of wood with structural steel
materials and their mechanical properties.
The exclusive brand-new polyester resin coating system
SHIMOCO (free of hexavalent chromium and heavy metals)
is formulated to allow the best UV and corrosion resistance,
guaranteeing maximum flexibility and durability, while having
sophisticated and intrinsic aesthetic qualities thanks to the
composition and textural pattern of the paint itself.
Thanks to these features, it is particularly suitable for roofing
applications and also for cladding and façades.
Marcegaglia: flat universe
Today Marcegaglia has a well-established presence in
the flat steel products sector (both carbon and stainless
steel), including the manufacturing of heavy quarto plates
and pre-painted products. It is a key international player
capable of supplying not only other service centres but
also specialised customers with a wide range of products
in terms of steel grades and applications: a unique range
of services with quick response times thanks to its stock
availability in standard sizes.
Last but not least is the efficiency of the distribution
network connecting the manufacturing plants with
each other and with customers: 11 logistic intermodal
terminals (or hubs) strategically located in harbours on the
Mediterranean Sea, the Atlantic Ocean, the North Sea and
the Baltic Sea, as well as storage areas near important
railway connections, significantly cutting delivery times
as well as carbon emissions, and enhancing flexibility and
service.