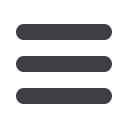

42
N
ovember
2013
Technology News
www.tubotech-online.com www.neftegaz-online.com www.valve-world.net www.tube-southeastasia.com www.tube-arabia.com www.tube.de www.tube-india.com www.tubechina.net www.tube-russia.com www.valve-world.net www.valveworldexpoamericas.comAMERICAS
www.valveworldexpo.comExpertise in
Flow Technology
Trade Fairs
Messe Düsseldorf GmbH
P.O. Box 101006
40001 Düsseldorf _ Germany
Tel. +49(0)211/4560-01
Fax +49(0)211/4560-668
www.messe-duesseldorf.devwe1402_FT_87x260_INT.indd 1
09.09.13 12:20
Weld seam
detection on
precision steel
tubes with low
error rate
THE position of a weld seam has a crucial influence on the
quality of the final product when bending or hydraulic forming
a tube. An unfavourable seam position causes deviations in
geometry, has influence on the firmness and in the life span
of the produced component or precipitates by cracking during
the manufacturing process.
In order to prevent such disadvantages, different solutions
for the localisation of the weld seam were established.
Common optical procedures, such as colour marking of
the longitudinal welds in order to detect their position, are
widespread. Camera-based systems, which detect the visible
welding seam are also in use.
What to do, if colour marking is not possible or the welding
seam is not visible? This problem arises when an application
requires a treatment of the tube after welding, for example in
the production of precision steel tubes. The cold drawing of the
tubes changes the original surface and impedes the usage of
colour. If the tube is additionally annealed, the welding seam
may become invisible in its external appearance.
At this point Roland Electronic offers alternative techniques,
well known from the non-destructive testing of materials with
eddy current, magnetic induction as well as the magnetic
leakage flux method. All
these techniques have
the advantage of dry
functioning and without
significant
radiation
exposure.
This technique is
based on the crystalline
modifications of the
structure within the weld
seam. In the process of
welding ferromagnetic
steel, martensitic crystals are formed within the range of the
heat effect zone.
Since martensitic crystals hardly occur in the unwelded
structure, the welding seam is detected by the crystal structure
modification. The weld seam detector SND40 supports these
alternative techniques and offers high process reliability in
practical usage.
Tubes with scraped weld seam and calibrated diameter will
reach in the first detection run ratios of 99.9 per cent.
The error rates in detection with an SND40 system are
between 0 and 100ppm.
Roland Electronic GmbH
– Germany
Website:
www.roland-electronic.com