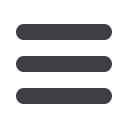

Technology News
www.read-tpt.com52
N
ovember
2013
Design and cutting of tubes
LANTEK has used all the experience
and proficiency gained in design systems
and programming for sheet metal cutting,
punching and bending machines and
applied it to the tube cutting sector
regardless of the type of machine.
Lantek Flex3d Tubes allows 3D design
in an intuitive and simple way, giving a
real vision of the result that the user will
obtain when cutting the profile on the
machine. It integrates different kinds of
tubular geometry importers: SAT, IGES
for example.
Lantek Flex3d Tubes is a parametric
system, allowing the user to change the
values of any of the operations made
previously; including the possibility of
changing the initial parameters of each
tube (lengthening, shortening, change
of diameter, etc).
Once the design stage is complete,
the user can simulate the optimisation of
the tube (nesting) and the path followed
by the cutting head, and directly
generate the NC program in order to
send it to the machine. Lantek Flex3d
Tubes adjusts cutting information based
on the characteristics of the machine
like the number of applicable axes (3
axis, 5 axis).
Technical characteristics include:
Lantek Flex3d Tubes gives a real vision
of the result on the screen. It displays
the exact tube and simulates in 3D
each process, reducing to a minimum
the possibility of errors; zoom, view
and rotation control tools allow for easy
manipulation and editing of the design;
Lantek Flex3d Tubes offers the user the
possibility of creating standard tubes
based on requirements; in addition to
cylindrical, rectangular and triangular
tubes, the user can design tube types
adapted to their needs from 2D outlines;
the 2D design options allow for the
design or import of desired geometry,
to create any type of cut out or trim;
dynamic coordinate system specific for
tubes. This tool offers various options
to configure the coordinate system; it
is totally integrated with Lantek Integra,
Lantek’s own ERP system; integral
management of the sales process from
the quotations through to invoicing. It
includes sales orders, manufacturing
operations, resource management,
material requirement, purchasing,
production planning and time and cost
control. It is also possible to incorporate
workshop data collection.
Integral management of warehouses/
stocks (profiles, sheet metal, tubes,
remnants,
commercial
product,
finished goods) includes serial and
batch numbers for entire traceability
management.
Lantek Flex3d Tubes allows the user
to obtain the best optimisation of the tube
and the generation of the NC file for the
machine. Optimisation can be created by
importing sections from the warehouse
automatically or by calculating the
needs of supply. The system allows the
user to locate in an intuitive way each
profile and subsequent operations along
the length of the tube.
Lantek Flex3d Tubes can simulate
the cutting machine and the sequence
over the tube. If the resultant simulation
is appropriate for the user, it will
automatically generate the NC file
for each machine and in the same
environment will integrate the information
related to the design and the post-
processing. Totally interactive simulation:
step-by-step, forward, rewind, pause and
restart.
For those tube cutting machines using
a 5X head, Lantek Flex3d Tubes offers
the option to automatically calculate the
machining in order to prepare the cuts
for the further welding process. This
option permits the user to define this
special machining technique, by means
of angle and distance.
Lantek Sheet Metal Solutions
– Spain
Fax: +34 945 298 714
Email:
info@lanteksms.comWebsite:
www.lanteksms.comServo positioning flag stop
system to speed up setup
THE new servo positioning flag stop
system from Manchester Tool & Die
Inc is designed to aid setup personnel
in quickly adjusting tube out through
the machine’s HMI (human machine
interface). This system will provide
consistent adjustments resulting in
quicker setup up times. The servo
positioning system is available for
newer M71 machines that are equipped
with HMIs. Manchester Tool & Die
supplies tube end forming equipment
and tooling to a variety of industries,
with machines ranging from 3/16"
to 3" OD capacities. Machines and
parts can be manufactured for special
applications.
Manchester Tool & Die
– USA
Website:
www.manchestertoolanddie.comCutting a hole with
the Lantek software