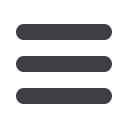

Technology News
www.read-tpt.com60
N
ovember
2013
New waterproof ‘C-Clamp’
encoder is versatile pipe
inspection tool
AN adaptable device which is ideal for
encoding manual phased array weld
inspections on pipes and tubes has
been launched by Phoenix Inspection
Systems.
The C-Clamp Encoder, which is
also suitable for linear array corrosion
mapping, is compact and very simple
to attach, requiring no tools for set-up
and operation. It is robust and precise,
offering high-resolution encoded scans,
and can be used for any single-axis
inspection.
The two clamping arms separate by
up to 55mm to fit around any of the vast
range of ultrasonic transducers and
phased array wedges on the market
today.
The arms can be quickly adjusted
to the wedge width and locked and
clamped into place with thumbscrews.
The waterproof wheel encoder can
be fitted either behind or alongside
the clamp, enabling B, C, D or S-scan
phased array data to be recorded with
its position.
The strong clamp mechanism
ensures no lateral movement during
scanning while the spring loading keeps
the wheel in constant contact with the
surface.
Andrew Brewis of Phoenix Inspection
Systems said: “The C-Clamp Encoder
is a small accessory that should be in
every inspector’s toolkit. It enables
phased array inspections to be quickly
recorded for sizing defects and is
very simple to attach. It is robust,
incorporating our new waterproof, high-
resolution encoder. It complements our
existing range of scanners and tools that
aid operators in the field.”
Phoenix Inspection Systems
– UK
Website:
www.phoenixisl.co.ukPair of mills nearing completion
OLIMPIA 80 has two complete tube mills
in the finishing and pre-testing phase
at its headquarters in Piacenza, Italy.
Both lines are engineered to produce
carbon steel tubes. One is destined for
Russia to produce structural tubes, and
the other is headed for Spain for the
automotive industry.
The “blue” mill, for Russia, is the last
of three lines for the same customer,
one of the most important Russian tube
manufacturers. The first two are in com-
missioning and are destined to produce
structural andAPI tubes. Their capacities
are from 21 to 89mm OD and from 40
to 133mm OD. Both lines are complete
with fully automatic strip loading system,
quick roll change system for breakdown,
finpass and sizing sections, chamfering,
hydrostatic test with washing unit and
automatic packaging machine.
This last line is the smallest, for tubes
from 12.7 to 60mm OD, and thickness
from 0.8 to 3mm. The maximum line
speed is 150m/min and the HF welding
generator has 300kW power. Special
features of this line include a quick
roll change system for breakdown,
finpass and sizing sections, and a fully
automatic coil strip loading system,
which begins with a carousel with four
arms of 30t each and a special car for
automatic loading of each strip coil on
the double decoiler.
The largest “grey” line, destined for
Spain, is for round, square and rectangle
sections, from 41 to 130mm OD,
thickness from 1.2 to 6mm. It is designed
to produce tube in high tensile strength
steel for the automotive industry. In this
case the maximum line speed is 120m/
min and the HF generator is 500kW.
As with the previous line, it is also
equipped with quick roll change system
for breakdown, finpass and sizing
sections, automatic loading system, and
an automatic system for the load of each
strip coil on the double decoiler.
Both lines have been pre-tested at
Olimpia’s headquarters, and are in
the process of disassembling for truck
loading and subsequent commissioning.
Olimpia 80 Srl
– Italy
Fax: +39 0523 864584
Email:
olimpia@olimpia80.comWebsite:
www.olimpia80.comPhased array weld
inspection