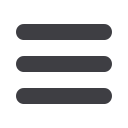

T E CHNOLOG Y
44
MAY 2017
Fast finishing of aluminium die castings
FOR high-volume production of complex
aluminium die castings, Kovolis Hedvikov
is a partner to car manufacturers and
their suppliers. To expand its capacity
and achieve more flexibility in the overall
manufacturing process the company
purchased a new vibratory finishing
system that can handle a wide workpiece
spectrum and was custom engineered
to fit into the available space at the
customer’s premises.
Kovolis produces components from
nine different aluminium alloys and
weighing between 200g and 8kg, using
casting technologies such as vacuum
investment casting and rheocasting.
The product range includes brakes,
power steering systems, turbo chargers
and compressors for air conditioning
systems. The company also provides
services for machining, heat treatment
and surface finishing.
With a trend towards larger and more
delicate components, which require a
vibratory finishing step after punch de-
burring for their downstream handling,
the existing finishing system was not
suitable and had also reached the
end of its productive service life. The
new system had to cope with larger
workpieces, and the finishing process
also had to be gentler.
The Rösler continuous feed vibratory
finishing system met the technical
requirements and Rösler could also
supply the necessary compounds and
finishing media. The new finishing
system consists of a linear feed
machine, type R 550/4600 DA, with a
usable length of 4.6m. The functions of
the existing loading system and hot air
belt drier were integrated into the overall
system controls.
Around 30 different workpieces with a
maximum diameter of 300mm (12") are
currently processed in the R 550/4600
DA. As it can handle parts with diameters
of up to 400mm (16"), the machine offers
flexibility for the future.
Depending on their individual
design, the castings are fed into
the finishing system at cycle times
between 30 and 60 seconds. The
single curve U-shaped cross section
of the processing channel ensures
optimum movement of the media and
workpieces through the machine. With
the use of high-performance plastic
media, this design produces finishing
results within a maximum processing
time of eight minutes. This time can
be adjusted by simple inclination of the
processing bowl. The undersize media
classification system is equipped with
an adjustable bar screen that allows
Kovolis to decide at which dimensions
undersize media must be discharged.
Since the finished die-castings do
not undergo a separate cleaning step
for removal of media fines from their
surface, the separation unit is equipped
with a spray-rinse station.
Rösler Oberflächentechnik GmbH
–
Germany
Fax: +49 9533 924 300
Email:
info@rosler.comWebsite:
www.rosler.com