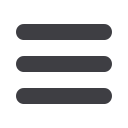

T E CHNOLOG Y
52
MAY 2017
Length and speed measurements for
non-destructive testing with laser precision
By Polytec, Germany
TO provide quality testing of steel
tubes, a suite of non-destructive testing
techniques are combined to facilitate a
fast and complete assessment of the
tubes.
Where length and velocity measure-
ments on rotating tubes are needed,
laser surface velocimeters are used
to provide critical position data during
the testing procedure. Inspection
facilities include processes suitable
for non-destructive testing of seamless
steel tubes such as electromagnetic
inspection, magnetic powder inspection
(MPI), metallurgical tests and ultrasonic
testing.
Depending on the application and
specifications, ultrasonic testing is applied
over the whole length and perimeter
of the tube for a comprehensive failure
analysis. Testing of both longitudinal
and transverse defects as well as
the inspection of wall thickness and
lamination are critical for quality control.
In order to track defects through the
machine the defect detection method is
combined with a position measurement
technique to eventually mark the defect
upon exiting the machine for further
processing. Laser surface velocimeters
are a solution for precise and reliable
tracking of the defect
position through the ma-
chine, without contacting
the surface.
Laser surface velocim-
eters (LSVs) use the laser
Doppler principle to evalu-
ate the backscattered laser
light from a moving object
and to determine the exact
motion and position of a
tube in the test stand. The
combination of methods
provides a fast and
complete testing of the tube.
A series of laser surface
velocimeters are used at
the ultrasonic test stand
to measure length and
velocity of the tubes. The tubes that are
passing through the facility are rotating
with a speed of 2m/s. Each inlet and
outlet of the stand is equipped with two
LSV sensor heads. Uniquely, with the
LSV is its possibility to detect the speed
component in the direction of its current
measurement. By using two correctly
aligned LSVs, the longitudinal and lateral
(rotational) motion of the tubes can be
distinguished and clearly derived. The
paired sensors at the inlet and outlet
of the ultrasonic test stand provide
measurement data for determining the
tube’s position while travelling through
the stand. The translational speed is quite
low in relation to the rotational speed.
Thus, the respective sensor head
must be aligned exactly parallel to the
direction of motion in order to avoid any
superposition with the lateral motion.
Otherwise the translational speed would
be influenced, causing errors in length
and position measurements.
The precise alignment of each sensor
is achieved by using a high precision
mounting plate and by following a
special adjustment procedure. With
the aid of precision screws the angular
position can be set precisely before
starting routine operation. Non-
contact and precise laser surface
velocimeters, combined with suitable
accessories, provide precision length
and speed measurements even in the
case of superimposed motions with
very different speeds. This measuring
technique allows the user to control
the forward and rotational movement
of tubes during non-destructive testing
with maximum precision and therefore
helps to optimise the overall process
performance.
The LSV emits two laser beams,
which overlap at a certain distance – the
working distance. The volume in which
both laser beams are superimposed is
called the measurement volume. In the
measurement volume the overlapping
laser beams generate an interference
pattern of bright and dark fringes. The
distance between those fringes is called
the fringe spacing and is a system
constant for the LSV. It depends on the
wavelength of the laser light and the
angle between the laser beams.
If a surface moves through the fringe
pattern then the intensity of the light
scattered back is modulated between
bright and dark. As a result of this a
photo receiver in the sensor generates
an AC signal. The frequency of the
signal is directly proportional to the
velocity component of the surface in
measurement direction. This makes
laser velocimetry a useful technology for
a highly reliable control process leading
to a cost-efficient manufacturing of
tubes and pipes.
Polytec
– Germany
Website:
www.polytec.comLSV measurement principle
LSV 2000