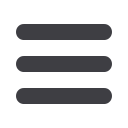

News
Technology
July 2015
37
www.read-eurowire.comThere are many factors that have
contributed to manufacturers moving
from copper to toward aluminium for
many automotive applications. Today
aluminium is used in primary cable and
power/battery cables for passenger and
commercial vehicles.
The justification for going to aluminium
is reduced weight, which provides up to a
47 per cent mass reduction compared to
copper. This can result in improved fuel
economy, easier assembly and cabling
that is easier to handle.
In addition, copper prices are much more
volatile. Aluminium is abundant and
copper is getting more difficult to find.
This, coupled with the pressure being
placed on copper demand from other
industries, gives the manufacturer a much
more stable supply chain and cost source.
However, there are other factors to
consider when using aluminium. For
example, the conductivity of aluminium
is approximately 60 per cent of copper.
Therefore the conductor cross section
has to be increased for the same current
capacity. There are also other factors such
as tensile strength, thermal expansion
and thicker oxide layers. Regardless, the
future of automotive cables is moving in
this direction.
The finished conductor sizes are typically
0.75 to 2.5mm
2
for primary cable and 3 to
160mm
2
for intermediate power/battery
cables. To produce these conductors there
are several steps in manufacturing. Firstly,
the small wires need to be produced.
Typically these are made on a Frigeco
multi-wire line, a single row of 16 wires
with 100mm capstans. Once the wires
come off the multi-wire machine and
onto reels they need to be twisted into
small bunches or sub units. The preferred
method of production of the small sub
units is to pay them off into a double twist
buncher (typically 630mm or an 800mm).
Depending on the number of wires
required in the sub unit and the number
of wires that can be processed on the
multi-wire, the number of payoffs required
needs to be determined. Once the sub
units
are
assembled,
the reel holding the sub
unit is either sent to
insulating, if the desired
cross section has been
reached,
or
multiple
reels coming from the
bunchers are placed into
driven, dancer controlled
payoffs and assembled
into a larger cross section
using a larger single
twist cabler. There are
many constructions that
can be used. The following are some
of these conceptual constructions and
are not intended to reflect preferred
constructions. The final construction
is determined to meet a specific
requirement as determined by the
supplier and the final customer.
A typical construction on the Frigeco
machines for 160mm
2
would be – 798
wires of x 0.51mm – 17.9mm Cond OD.
This is made of 19 sub units of 42 wires
of 0.51mm diameter and assembled into
a 1+6+12 to produce the final conductor.
First the 0.51mm wires are made on the
multi-wire as above. These sub units of 42
wires are assembled on a Frigeco double
twist buncher.
Once the sub units are assembled, the
bobbins are placed into 19 driven dancer
controlled payoffs to produce the larger
conductors. Each of the payoffs has a
motor and the speed of the bobbin is
controlled with the pneumatic dancer.
These individual units are assembled
using a lay plate where the sub units
are arranged in a 1+6+12 symmetrical
orientation and placed into the 1,600mm
single twist cabler to produce a very high
quality unilay construction.
Once the primary or battery cable
conductor is produced, it must be
insulated. These insulated conductors
need to meet the hostile and demanding
requirements of the engine compartment
where the temperature can range from
-40 to +180ºC.
Mario Frigerio SpA – Italy
Website
:
www.mariofrigerio.comFrigeco to the automotive rescue
▼
▼
A Frigeco multi-wire line