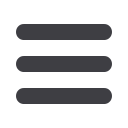

News
Technology
September 2016
49
www.read-eurowire.comThe photovoltaic industry has been
going through a rapid change over
the last decade. In addition to growth,
the industry has continued to witness
relentless price pressures along the
PV value chain. The same is the case in
the PV ribbon industry. Only PV ribbon
producers that kept consistent product
quality whilst maintaining low cost base
and efficient production process have
remained competitive.
Plasma-based annealing and tinning
process represent an efficient PV ribbon
production solution that will ensure
consistent, top quality finished products
at low cost.
Plasmait from Austria has introduced a
new PV ribbon annealing and tinning line
designed for high output production. The
new line features a maximum production
speed of 210m/min. This allows the
line to produce up to 250 tonnes of PV
ribbon per annum in a typical production
split between interconnect and bus bar
ribbons.
PV ribbon lines can produce a wide range
of interconnect ribbons and bus bars in
a typical size range of 0.8 to 8mm wide
and 0.1 to 0.5mm thick. The ribbons
are usually coated with 20 micron thick
layer of solder with a coating thickness
tolerance of ±3 microns. The new line can
produce ribbons of various yield strength,
typically with Rp0,2% between 50MPa
and 90MPa.
Copper ribbons are paid off from a 500kg
spool with finished tinned PV ribbon
being spooled onto 4-10kg spools in a
continuous production. The single-head,
precision layer winding spooler includes
an accumulator to ensure uninterrupted
production during spool changeovers on
the takeup side. Some producers choose
to equip the line with an automatic spool
changeover unit that can be integrated
with the takeup unit. Multiple lines can
therefore be operated with a single
operator, which reduces labour cost.
The PV ribbon line can also be integrated
with an in-line rolling mill to produce
interconnect ribbons directly from round
copper wire. A single- or double-stand
rolling mill can be used for in-line
operation subject to required size and
tolerance of the finished ribbon.
Unlike traditional tinning processes,
plasma tinning lines operate without
chemical cleaning and fluxing whilst
rolling runs without cooling agents. This
makes the whole production dry and
environmentally friendly.
Flux-free plasma tinning process avoids
contamination of tin bath with flux, which
makes a big difference in the cost of tin
waste. Average annual savings in terms
of tin waste alone is as high as €100,000
per line when compared to the traditional
flux-based tinning process. This does not
take into account the savings a PV ribbon
producer yields from reduced scrap rates.
The new line allows PV ribbon producers
to reduce labour costs and scrap rates
whilst improving production consistency
and product quality. It also features low
energy use and maintenance cost per kg
of finished material. This combined allows
the new PV ribbon line to claim the lowest
cost of PV ribbon production overall,
according to Plasmait.
The new line can be equipped with specially
designed wiping system for round wires for
production of a new type round PV ribbons
that have recently been introduced.
Plasmait GmbH – Austria
Website
:
www.plasmait.comNew PV ribbon and tinning line