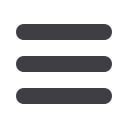

the diaphragm diameter and, with that, also the
process connection.
To address this problem, the company has
developed a new pressure gauge for small external
areas: The model PG43SA-C measures in the low-
pressure ranges with a proportionately much smaller
diaphragm. This instrument combines the reduced con-
nection size with a further specific feature that is particularly im-
portant for such measuring requirements on tanks: It is autoclavable.
The pressure gauge can be sterilised with the vessel under saturated
steam conditions at temperatures up to +134°C, without needing to
be dismounted. The process thus remains sealed, also in the mobile
phase, and the quality assurance is preserved.
Conclusion
The more critical the pharmaceutical process – for example, produc-
tion of injection materials – the more important is the consistent
maintenance of the sterile boundary in the manufacturing process.
Risk prevention has, with the measurement technology used, an
equally high requirement as accuracy and reliability of the process.
The particular challenge is to merge the technical functionality and
physical design features into an economical solution. For pharma-
ceutical processes are getting increasingly more efficient in view of
the competitive situation – but without ever compromising safety.
dresses these issues: A diaphragm seal system
with a dual diaphragm and diaphragmmonitor-
ing removes the risks and the consequential
damages as described. Using this patented
system, the space between the two diaphragms
is evacuated and the vacuum can be monitored with
a measuring instrument.
The type of monitoring can be specified individually, de-
pending on the sensitivity of the process. With regular on-site visual
inspection, for example, it is sufficient to check a pressure gauge
with green-red display, in other cases an optical or acoustic alarm
in the control room may be required. When using media with a high
risk potential, the operator can use a pressure switch which will im-
mediately halt the process in the event of any damage.
Should the wetted diaphragm become damaged, the second
diaphragm forms a reliable seal to the process and maintains the
pressure monitoring until the damage has been rectified. Since a
break within the system is detected and reported immediately, no
microbes can get past the diaphragm undetected. Other options are
available which can mechanically or electronically identify a failure in
the diaphragm seal. If a seal is broken during maintenance or calibra-
tion the operator will immediately see this condition and will prevent
a defective unit from being reinstalled. Furthermore, the ‘alarm’ is
reported immediately in the event that the diaphragm is damaged.
This prevents a defective instrument being installed in the process.
The safety function of this self-monitoring diaphragm seal system
simultaneously optimises the protection of the non-process side: In
the event of a damaged diaphragm, no dangerous substances can
escape into the environment.
When a company uses such a device it shows due diligence that
the system is monitored through an automated system and is not
left to manual inspection of a seal area. In spite of the extremely high
level of automation in pharmaceutical processes, not everymeasuring
point absolutely has to be catered for electronically. For such cases,
diaphragm pressure gauges with flush diaphragms are particularly
worthwhile. These enable the measurement of low pressures and
are exceptionally safe in overload as a result of their design. They
keep the process sealed, even with pressure surges. Nevertheless,
operators can also prepare themselves for the case of any possible
damage to the diaphragm element. For such pressure gauges, the
company also offers diaphragmmonitoring, which will immediately
indicate any rupture in the pressure element.
Diaphragm pressure gauges are suited mainly for mobile tanks,
in which intermediate and end products are stored or transported to
the next processing stage. They monitor, for example, the filling and
the inert gas blanket. The dimensions of such containers are getting
smaller and smaller, as the pharmaceutical industry is increasingly
turning to the development andmanufacture of individual medicines.
Processes with small units and batches are the result. The measuring
instruments for the corresponding tanks therefore have limited space
available. This can quickly become tight for diaphragm pressure
gauges: The lower the pressure to be measured, the larger must be
DRIVES, MOTORS + SWITCHGEAR
P ESSURE + LEVEL MEASUREM NT
take note
Joachim Zipp is the Global Market Segment Manager Food
and Pharma at WIKA, Germany.
Enquiries: WIKA Instruments. Tel +27 (0) 11 621 0000 or
• Pressure measuring instruments are subject to the highest
safety criterion: The protection of consumers.
• Damage to instruments occurs for various reasons and
could lead to product contamination.
• A special solution which addresses all the risks has been
developed.
31
January ‘17
Electricity+Control