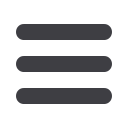

106
Wire & Cable ASIA – September/October 2014
www.read-wca.comNot only does theory ignore the elastic deflection of hooks,
it also ignores the plastic deformation that occurs before
the elastic limit of the body coils is reached.
If the elastic limit of body coils is defined at a loss of 0.1N,
then part of this loss is due to the plastic deformation of
the end hook.
Indeed the results show in
Table 1
that when 0.1N is lost,
the free length has increased by 0.015mm, which equates
to more than ten per cent of this load loss.
The actual load/deflection graph to the load at which there
is a 0.1N loss is shown as
Figure 4.
The stainless steel springs were processed in a similar
manner to the carbon steel except that they lost load at
much smaller deflections.
The results are shown in
Table 3
.
The spring rate increased slightly as the LTHT temperature
was increased despite the outside diameter increasing.
This is because the torsional modulus, G, increases with
the heat treatment temperature, as shown in the European
Standard for stainless steel spring wire, EN 10270‐3.
LTHT /
°C
Initial
Tension
N
% Rm
Load at
which 0.1N
loss
% Rm
Load at
which 0.2N
loss
% Rm Spring
Rate N/mm
Outside
Diameter
mm
‐
9.15
14.2
17.6
27.3
19.6
30.4
0.810
6.13
150
6.77
10.5
24.3
37.7
26.5
41.1
0.840
6.10
200
6.16
9.5
26.8
41.5
28.8
44.6
0.850
6.06
250
5.12
7.9
26.6
41.2
28.6
44.3
0.850
6.03
300
3.72
5.8
25.0
38.7
27.2
42.1
0.856
6.03
350
2.16
3.3
24.0
37.2
26.0
40.3
0.881
6.03
Load / N @
Load/ N @ 30mm
Free Length /mm Loss of load /N @ 30mm
9.15@ 30mm
9.15
25.005
0
17.61@ 40mm
9.13
25.010
0.02
21.81@ 45mm
9.12
25.020
0.03
24.33@ 48mm
9.10
25.020
0.05
26.00@ 50mm
9.07
25.020
0.08
27.63@ 52mm
9.02
25.020
0.13
29.23@ 54mm
8.91
25.030
0.24
30.80@ 56mm
8.72
25.030
0.43
LTHT / °C
Initial
Tension
N
% Rm
Load at
which 0.1N
loss
% Rm
Load at
which 0.2N
loss
% Rm Spring Rate
N/mm
Outside
Diameter
mm
‐
5.78
11.3
12.7
24.7
14.5
28.2
0.740
6.12
200
5.30
10.3
15.4
30.0
17.4
33.9
0.750
6.12
250
4.90
9.5
16.3
31.7
18.2
35.4
0.760
6.13
300
4.65
9.1
16.6
32.3
19.2
37.4
0.767
6.12
350
4.35
8.5
16.6
32.3
19.0
37.0
0.770
6.13
400
4.00
7.8
15.6
30.3
18.5
36.0
0.765
6.14
450
2.85
5.5
5.3
29.8
18.2
35.4
0.770
6.14
❍
❍
Table 3
:
Results for the 302 stainless steel springs
❍
❍
Table 2
:
Results for the carbon steel springs
❍
❍
Table 1
:
Example result for a carbon steel spring heat treated at 250°C
❍
❍
Figure 4
:
Load/Deflection characteristic of a carbon steel
extension spring heat treated at 250°C