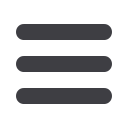

NS-EN 474-1 :2006+A3:2013
EN 474-1 :2006+A3:2013 {E)
b) It shall be possible to verify from the operator's station, or from the location where the engagement system
of the attachment bracket is operated, that the system has activated successfully into the engaged
position.
c) It shall not be possible to release the attachment by malfunction or loss of engagement force(s). For the
purpose of testing, the attachment shall not be released with the machine switched off for a period of at
least 12 h.
8.2.1.2
Locking
In addition to 8.2.1.1, the attachment bracket shall have a locking system that meets the following
requirements:
a) It shall ensure that the engagement system remains effective and holds the attachment in the intended
operating position, considering reasonably foreseeable operating conditions (see 7.2, 8.2.4 , and any
relevant limitations specified in the operators manual of the machine manufacturer, and if relevant the
attachment bracket manufacturer and/or the attachment manufacturer).
b) For attachment brackets which are engaged via the controls at the operator's station it shall be activated
automatically as part of the engagement process.
c) For attachment brackets which are engaged manually it shall be activated manually from the location
where the engagement process is conducted or as an automatic action during the engagement process.
d) An automatic locking system shall have either an automatic or a manual unlocking system.
e) For wedge type systems, in the event of a failure of the system that provides the engagement forces, the
locking system (e.g. continuous pressure with open return, hydraulic accumulator, compressed spring)
shall be able to withstand the resultant of all reasonably foreseeable forces applied to the attachment.
NOTE 1
Reasonably foreseeable forces will depend on the type of attachments used. For requirements,
see e.g. ISO 14397-2, ISO 10567 and ISO 6015.
f)
For force locked engagement systems, in the event of a failure of the system that provides the "-"""
engagement forces, the locking system shall be able to withstand the resultant of all reasonably
foreseeable forces applied to the attachment. This shall be achieved by a mechanical device not relying
on hydraulic pressure.
NOTE 2
Reasonably foreseeable forces will depend on the type of attachments used. For requirements,
see e.g. ISO 14397-2, ISO 10567 and ISO 6015.
8.2.1.3
Restriction of engagement and locking system design
A design with engagement from the operator's station in combination with locking at the attachment bracket is
not permitted.
NOTE
This prevents the unintended detachment of the attachment caused by non-use of the locking mechanism.
®.1
8.2.2 Control
For the actuation of a hydraulically operated locking and unlocking system of an attachment bracket,
preferably a separate control shall be provided.
The control shall be secured against inadvertent activation (see 5.5.3).
If the actuation is integrated in a control, which is used for other functions than locking/unlocking the
attachment bracket, the following requirements shall be met:
39